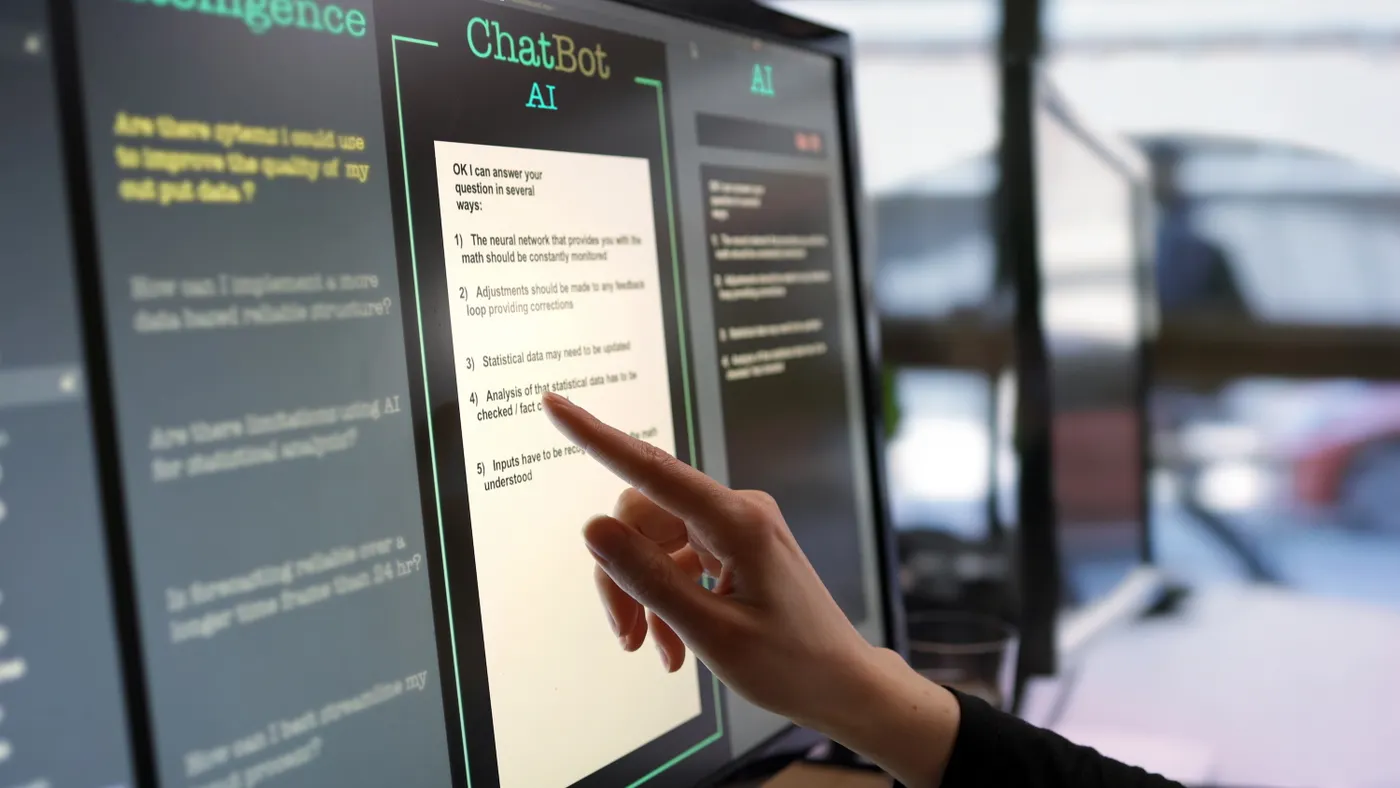
Agentic AI is the new tech buzzword. Here’s what builders need to know.
Three months into 2025, the artificial intelligence arms race continues for builders. Large contractors, such as London-based Balfour Beatty and Swedish builder Skanska, are developing their own AI-based tools to aid their construction processes.
Other builders use tech solutions that come from vendors. Marietta, Georgia-based Cork Howard, for example, uses Billy the Bot, named and created by Mountain View, California-based software firm Stampli. With the tech, the team is able to cut down on the time, effort and focus necessary to track the litany of invoices that the firm receives and needs to process on any given day.
It’s not just finance, either — AI and its uses were the talk of the expo at Engineering News-Record’s FutureTech conference in 2024, where builders discussed how they used it to check contracts for compliance and increase jobsite safety.
Now, the next iteration of AI is knocking on the construction industry’s door — agentic AI. A type of artificial intelligence that tech giant Nvidia claimed in a Jan. 6 blog post will act as a “knowledge robot,” the tech holds the promise to help companies across industries, not just builders, automate their work. But whether the buzz around it is just hype or has real potential can be difficult for builders to parse as they consider its uses in their day-to-day work.
What is agentic AI?
Agentic AI is an evolution of generative AI — it’s still trained on specific data sets, and users can still interact with it via a chat or prompt. However, what sets the tech aside is its ability to act autonomously.
“Agentic AI represents the next wave in the evolution of generative AI. It enables applications to move beyond simple chatbot interactions to tackle complex, multi-step problems through sophisticated reasoning and planning,” Nvidia wrote.
In other words, agentic AI takes that answer a step further.
For example, a builder might ask a generative AI bot to figure out how much money it owed to a specific concrete subcontractor in 2024. The bot would answer that query based on that single interaction.
By contrast, agentic AI could create a plan around the bills and invoices autonomously, with the human taking action.
Barry Mostert, tech giant Oracle’s senior director of artificial intelligence and analytics, wrote in a Feb. 10 blog post that agentic AI puts the construction industry “on the brink of a transformative leap.” AI agents could help builders improve safety, optimize their costs and proactively mitigate risk, Mostert claimed.
Patrick Murphy, the CEO of estimating and takeoff software creator Togal.AI, said that an agentic AI chatbot could operate much like an employee.
“For example, instead of asking an AI to write a few plans and then reviewing them yourself, you could tell an agentic AI to generate multiple options, analyze all the data, select the best one, and even propose new ideas based on current market trends,” Murphy said. “Then, it could check back in 48 hours with a full report.”
Worth the hype?
Although some analysts expect businesses to quickly reap the rewards from AI agents, others are expressing caution, specifically regarding security concerns, CIO Dive reported in January.
“Even though it might be overhyped in the first year, we’re going to be seeing some interesting results this year and also probably some epic failures,” Vladimir Lukic, global leader of Boston Consulting Group’s Technology and Digital Advantage practice, told CIO Dive.
Senthil Kumar, the chief technology officer for Slate Technologies, a contech firm that creates AI tech for the real estate, building and investment industries, is taking a more measured approach. Kumar noted that AI in construction is full of failed full-automation promises, but that the tech could help contractors who carefully implement it get a let up on their peers.
Kumar said that agentic AI could, for example, help builders manage their schedules, manage risk and compliance, optimize how resources are used and anticipate supply chain disruptions. But knowing that it isn’t a technological cure-all is important.
“There is of course no magical overnight transformation and if one is expected, people will be disappointed,” Kumar told Construction Dive via email. “Those integrating this AI strategically, will gain a significant competitive edge.”
Indeed, other experts are far from certain of agentic AI’s potential, and outright doubtful of its capabilities at present.
“We conducted a thorough review of AI agents in production, analyzing their goals, operational mechanisms, and the extent of their autonomous behavior,” Craig Le Clair, principal analyst at Cambridge, Massachusetts-based market research firm Forrester, told CIO Dive in an email. “Basically, most agents are far from agentic. This is the future and does not yet exist.”
Not on autopilot
Kumar also warned contractors about potential red flags that they could come across from vendors who might be selling a product that isn’t a good fit.
These range from an AI system that can’t explain its output or an improper integration strategy, to overpromised return on investment or a guarantee of full autonomy. An optimal system, Kumar said, needs human-in-the-loop oversight.
“Selecting the wrong vendor, adopting suboptimal technology, or executing a flawed implementation strategy can result in operational inefficiencies, unrealized potential and wasted investments,” Kumar wrote.