In the building industry, convergence is a blurring of lines between technology, process and sectors such as architecture, manufacturing and entertainment.
The goal? Finding better ways to design, build and make space.
“Architects and builders are looking to manufacturing to make the construction process more like industrial assembly lines — modular, repeatable and efficient,” Autodesk University writes. “And they’re finding ways to use standardized parts and digital tools to improve safety and accelerate project timelines.”
As VP Industrialized Construction at Autodesk, Amy Marks says construction business models are shifting to meet demands from a growing client segment called “convergence customers.”
“When you think about what a convergence customer needs, it's very different than what just a general contractor needs, or just an architect needs, or just an owner needs, or just a building product manufacturer needs,” says Marks.
“They need a platform of connected data. They need the interoperability between many different ecosystem partners, whether that's in services, or technology, or products. They're looking across the silos — they're basically burning them to the ground at this point. And I think that changes everything.”
During her keynote address at the Advancing Prefabrication 2022 conference, Marks said 82% of the audience considered themselves convergence customers.
But they’re not explicitly asking for convergence solutions, Marks notes.
Rather, clients tell her they are looking for integrated support because their business models are changing and “there are forces on my business, and the way in which I do business, and how I make money that have changed.”
So if a contractor responds to an RFP by offering up an evolved framework that incorporates a convergence of prefabrication, technology and advanced processes, the customer feels better enabled to achieve their project goals.
How convergence in construction actually works
Marks touches on two key ways convergence takes place in construction.
The first is a “horizontal” integration of different — but often adjacent — business types that merge, or incorporate another offering, to increase their shared value. “Architects are buying [pre]fab shops, and general contractors are becoming makers and makers are becoming designers of things,” she explains.
We’re seeing “vertical” compression too, according to Marks. “Whether it's the GC or the mechanical, electrical or plumbing subcontractor, or the traditional building product manufacturer — they are merging together as makers.”
For example, she describes how an electrical contractor might not actually produce anything that’s included in the electrical skids they supply.
Instead, they function as a “product and system integrator” of the manufactured items provided to clients. Or the building product manufacturer who creates those items offers the entire skid as an aggregated solution.
If you think bigger, Marks says, this type of convergence can enable the creation of smart buildings and even whole smart cities that function as vertically integrated environments.
Envision future cities where “platform companies like Meta and Google own undersea cables to emerging geographies. The data center will be owned by them, the infrastructure that gets built around them potentially… I'm sure they would like it to integrate with their platforms down to the end use in their home,” says Marks.
“And so I think it's a very interesting conversation about convergence and platforms that's much more far reaching than we think.”
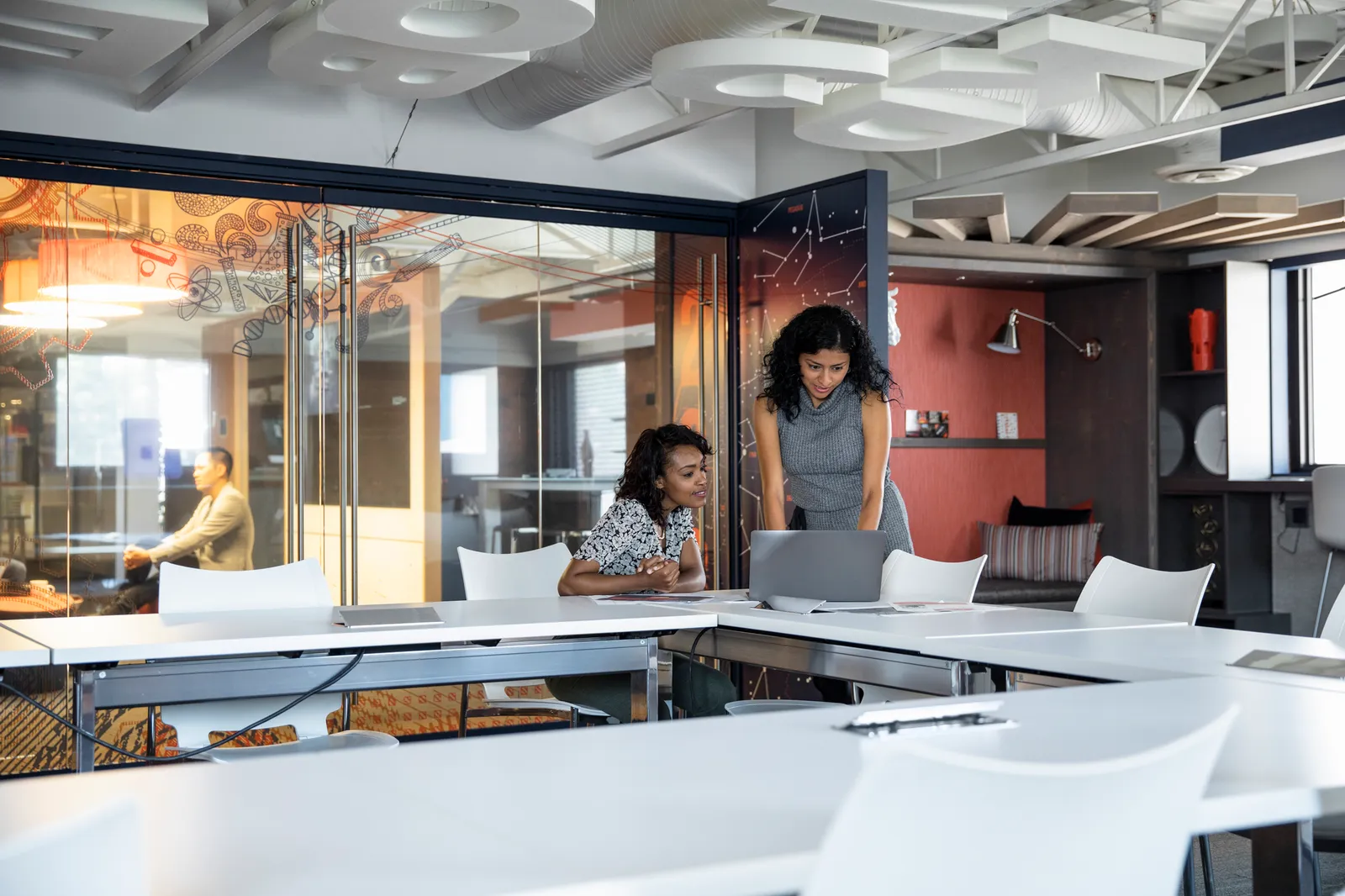
Shared context is key to evolve your business model
Merging previously separate industries or processes is not a simple task. To make it work, all the stakeholders involved must learn how to speak different languages (in a figurative as well as terminology sense) to bridge contextual gaps, Marks says.
“As you’re starting out and these business models are first changing, you have to understand the language of the genesis of the original core competencies. And then you have to understand the language of your adjacencies.”
For instance, “the DfMA in a manufacturing setting has different interpretations than DfMA may in an architectural setting. You're converging with and reconciling the [industry] language to make sure that you both mean the same thing.”
Merging with other specialties requires an appreciation of diversity and perspective to create shared understanding, and perhaps in the future, even a new language, Marks says.
Randee Herrin, Senior VP of Construction Technologies & Manufacturing at TDIndustries Inc., says her construction and facilities services company utilizes a “model-led workflow” to spark collaborative understanding.
With this approach, all stakeholders come together to make shared decisions earlier than usual in the construction process, producing a virtual model (thank you, technology) for the project.
“You have to step outside of just [your company], and engage the entire team — the general contractor and the owner or the other key subs — that means those decisions between the entire team need to happen earlier. And it needs to be much more cooperative and a partnership upfront, to have a better outcome at the end,” Herrin explains.
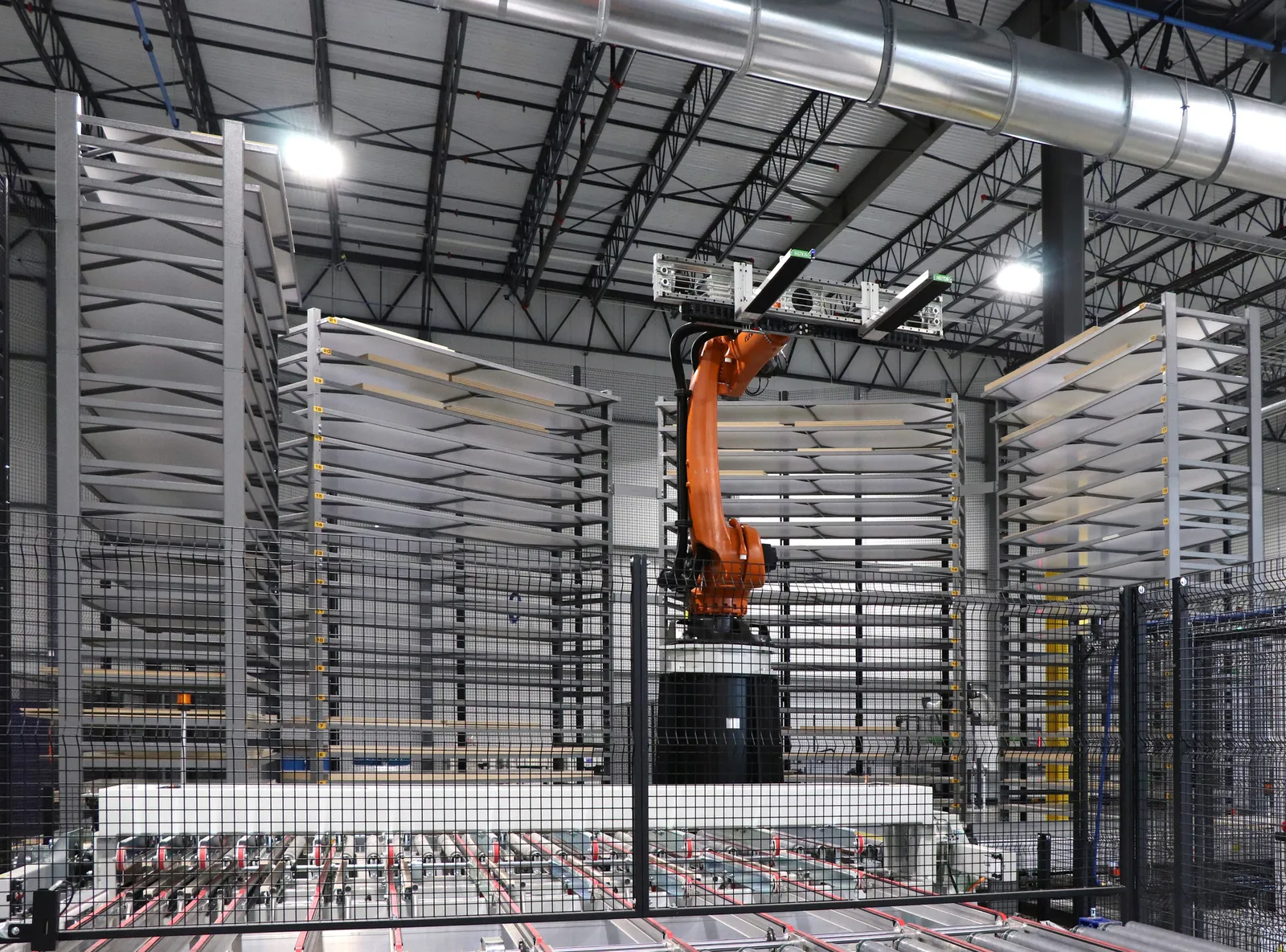
Perceptions of industrialized construction have evolved too
“The future is about data. It’s enabled by the [virtual] model and…by offsite manufacturing,” says Herrin, who thinks the construction industry is in the midst of a renaissance, as future-oriented firms rethink their approach to building spaces.
After all, who doesn’t want their job to be made easier and to access greater project certainty through data, she says.
“To me, it’s how many constraints can we remove? We're managing a workforce that's hard to find right now — a declining workforce. And we could sit with that problem or we could say ‘how can we solve it through off-site manufacturing?’”
In addition to the obvious benefits of industrialized construction, some old-school misconceptions are also being debunked, says Marks.
She scoffs at the idea that manufactured building products — a key element of construction convergence — are not considered beautiful or that architects and designers say, “I will not have prefab on my project.”
“Those kinds of things are so 10 years ago,” she says. Now there’s widespread interest and acknowledgement of industrialized construction. Project stakeholders just need help understanding how to incorporate prefabricated solutions into their construction plan.
One way or another, every building now incorporates manufactured products in construction, she points out.
“So yeah, I think at the end of the day, the word prefab won't exist. It'll just be products.”