Tracking the progress of structural steel erection on any job is paramount. One incorrect or misplaced beam can potentially put the whole project in jeopardy.
Yet, the problems with how firms track steel are manifold — some firms plunk data into an Excel spreadsheet, and there can be a discrepancy in data standards among stakeholders on a project.
Boston-based Suffolk Construction has a solution that it developed in house. Live Dimensions, created by Suffolk’s Director of Digital Engineering Denis Leff, utilizes BIM models to track steel progress from design through fabrication and final construction. It has already identified common pitfalls in the erection process, he said, saving the firm time.
In a news release, Suffolk said Live Dimensions uses artificial intelligence to parse datasets and standardize information into a unified database. That allows it to dynamically update the BIM model, which provides a real-time snapshot of a project’s structural steel status.
Secrets to success
Leff said that his interest in tech began when he spent time working for Samsung in South Korea — he worked from 2010 to 2016 as a BIM development manager at the company’s construction and trading division headquarters in Seoul.
Since moving on to Suffolk, Leff’s passion has been bringing BIM to the masses, even non-experts. Hence, Live Dimensions was born.
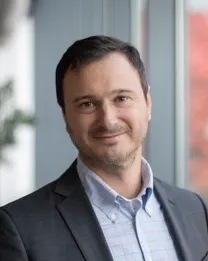
“BIM models hold all the information of what we're about to build,” Leff said. “And I see them generally as underleveraged in our industry, partially because the technology blocks a lot of people. They don't know how to access the data unless you're a BIM expert.”
Currently, Suffolk is using Live Dimensions on its South Shore University Hospital Pavilion Core & Shell project in Bay Shore, New York. The scope for the first phase of work includes abatement and demolition, site utilities and the full core and shell, according to the project’s information page. The $468 million project celebrated its steel topping out in October, and will be completed in the second quarter of 2026, according to the hospital network.
The program helped with two key issues on the build: tracking completion and deliveries. It kept the team from having to deal with piecemeal data entry into an Excel spreadsheet or using costly tracking software.
Instead, users simply dragged and dropped a BIM model into the program, marking it as ready to track. When steel was delivered, they then scanned the bill of lading from the delivery firm and uploaded it to Live Dimensions.
“Knowing where the material is and what state it is in to ensure continuity in the field is really important, because you don't just stop steel if the steel isn’t ready. You stop the entire project,” Leff said.
While Leff said it was too early to assess whether the tool can help with mitigating rework, it’s been useful in identifying, and tracking, the routine mishaps that can occur during the erection process, such as bolt hole misalignments and damaged beam replacement.
“A lot of this stuff is par for the course. It happens on every project,” Leff said. “But we're really trying to get an understanding — is it a project in New York? Is it a particular contractor? Is it a particular fabricator? Is this going to happen, more or less, with certain people that we partner with?”
A focus on innovation
Leff said he built the software in a six-month period before the company was going to put steel up on the South Shore project. With the help of Matthew Chen, a digital engineering intern for the contractor, Leff also turned Live Dimensions from an app into a web-based platform.
Suffolk’s focus on innovation made it easy to iterate the solution — the company has an in-house venture capital arm, Suffolk Ventures, which invests in construction technology across the building cycle.
“We're very tech-forward as an organization, so there's a lot of support for reaching our goals, our passions, if they fit the bill of moving our company forward,” Leff said.
If Leff were to build this program outside of the company, he said he’d be under more time constraints.
“Here, I'm able to understand the project's needs at a comfortable pace, try things out, reiterate, improve,” Leff said. “It's not like being an external person trying to create a solution for someone else. You have a little bit more time to do things thoughtfully, and that's why I'm going one project at a time.”