Mason Ford, the director of sustainability and equipment services at Skanska USA Civil, knows how hard it can be to eliminate safety incidents on construction sites.
Groups of people moving around the jobsite, heavy machinery with obstructed views in the cab and limitations on technology make it hard to pursue that goal. But, the 20-plus-year veteran of the construction industry still has some big ideas about how to make it happen.
Here, Ford talks with Construction Dive during Construction Safety Week about the technologies that Skanska uses on the jobsite, the roadblocks that make it hard to create an injury-free workplace and how the firm is overcoming them in its journey to zero injuries.
This interview has been edited for brevity and clarity.
CONSTRUCTION DIVE: What safety tech are you seeing on the jobsite today?
MASON FORD: Our current journey is to install blind spot detection on every machine that we own.
We're putting aftermarket or factory OEM technology on them. If we order a new machine, we order it with the new technology, the best they've got available, which for most of them is only identification. It's not avoidance.
You can get a loader from Caterpillar or John Deere or other manufacturers that have some great technology built into it. It may have artificial intelligence where it can identify a human being in its path, but it still doesn't automatically brake for that human being. It’ll still actually hit him.
I'd say that, without taking anything away from what we're doing and the effort we're putting into installing aftermarket technology right now, it's still just a Band-Aid.
I don't say this out loud a lot, but the reality is, even our push to put in our own equipment is more for moving the industry and doing our part, and saying, “Hey, we've put the best available technology on our equipment and it's still not enough.”
It sounds like you're really bullish on automation and automated heavy machinery. Does Skanska use it often?
We don't. Realistically, we see there's demand for it.
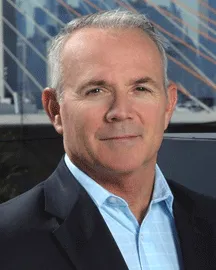
The construction field that we work in right now, where we're doing tight, urban-type projects, is probably one of the least open, or least productive, for automation.
If you're doing more greenfield work, where you're installing solar panels or wind turbines in a huge field with no human beings around, you have a lot better odds working with automation than when you're working on the side of a busy highway or in a densely populated area next to Newark, New Jersey’s Liberty Airport.
In those dense areas, then, how does Skanska keep workers safe?
In those spots, we’ve installed object detection, which is a big benefit. In select areas and select markets, we use video surveillance.
There's a bunch of automation in video surveillance, which includes watching a project and looking for any types of hazards, recognizing them and giving us opportunities to train workers. We show them what happened, where the near miss was and what could have been done differently.
Our journey is always toward zero. We wish that there weren't any incidents, but there are. If you're running video on every project, you see what every human being did, every instance across the entire U.S., you could probably break it down to have really good data about near misses.
What our journey has been like, is that we report near misses, and we've looked for them whether it's captured on video, or captured by a bystander or somebody who was participating in it.
But the journey toward getting good information on that has taken a long time because initially, people don't like to claim they had a near miss, or they don't completely understand what a near miss is. Our safety professionals have taken a great journey where we've gone to great lengths to define what those near misses are and provide good feedback rather than punishment for near misses.
That way, they continue to be reported properly and acknowledged, and used as training activities, rather than shoved under the rug or not reported.
What do you think will be the future of safety technology?
Some of what I talked about earlier about evolving the machinery is a real big step in safety. If you look at the makeup of a wheeled loader, as an example, so much of the obstructed view for people on the ground is the operator cab and the handrails.
There's a whole bunch of things related to the operator being on the machine that cause safety issues.
When you pull the operator off, you change the center of gravity of the machine, and make it not only more efficient, but able to perform its function with better visibility to and from the people on the ground.
What I hope to see evolve is the machinery and the construction process.