This is the third article in a series about the increasing importance of preconstruction since the COVID-19 pandemic. Read the first and second articles.
Technology has definitely played a role in preconstruction’s increased prominence in the overall build process today. But many experts see behavioral and process swings spurred by the pandemic at the root of systemic change for the industry.
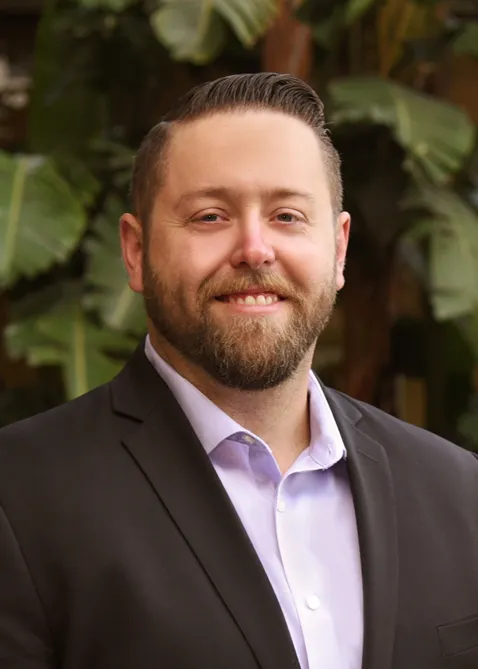
“Of course I wish there was a tool that can get us all to where we need to be, but there’s no tool,” said David Alford, regional vice president of preconstruction for St. Louis-based McCarthy Building Cos. “The development of broader trust and cooperation in the base relationship of the partners is what gets you there.”
That said, when it comes to how projects of the future will be managed during preconstruction — roughly the period from project conception to groundbreaking — there’s not just one established path.
Building construction “packages”
Even the idea of preconstruction having defined start and end points is starting to vanish as teams look to resource optimization. For example, teams might pull the trigger on certain trade packages (think supply-challenged power mechanicals) even as other portions of the project remain in the design phase.
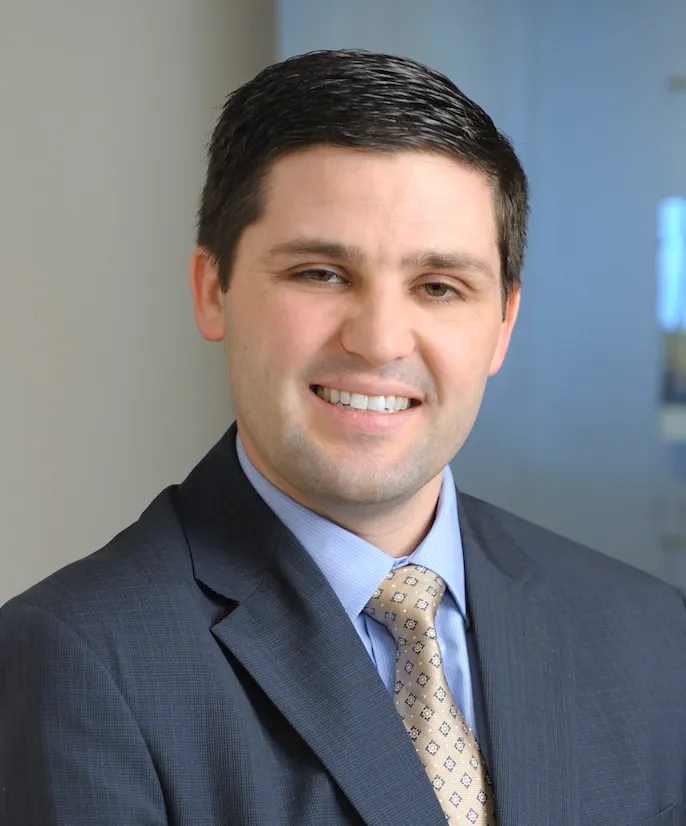
“On almost every modern project we are working in packages, from site work and foundations to enclosures and interiors,” said Nathan Lingard, director of design phase at Minneapolis-based Mortenson Construction. “The staging of starts into packaging allows us to advance certain parts of the design even while others are lagging. We almost always overlap construction. Project teams are starting to build while we are finishing design.”
Alford calls package delivery part of an intentional and necessary blurring of the lines that helps preconstruction better reach its paramount goal of optimizing the delivery of project scope on time and on budget.
“The idea that ‘Here’s traditional pre-con, hard stop, now here’s construction’ is becoming antiquated,” he said. “It’s actually our goal to make it blurry so that you don’t know one side from the other. You just know a project team that works closely alongside the designers and owners delivered an exceptional outcome.”
From pre- to post-construction
Robust data storage within BIM-enabled point clouds and change management platforms that can document decision-making along the way also stretches preconstruction collaboration beyond the construction phase into building operations and facility management.
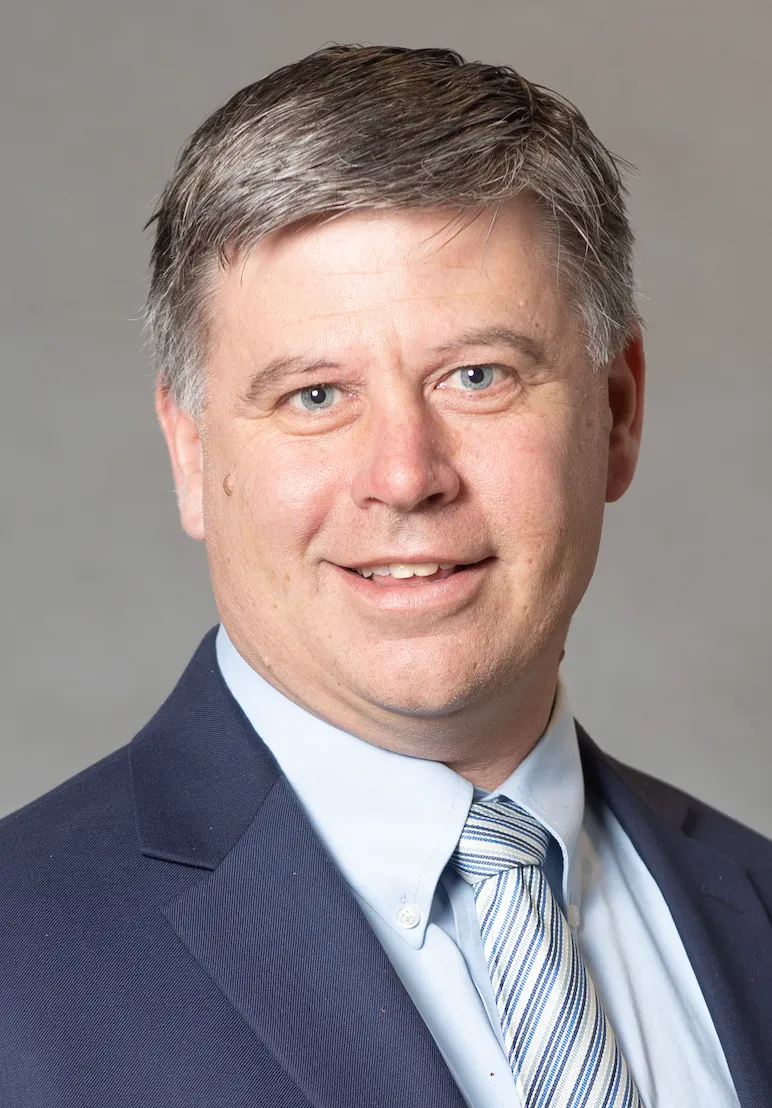
“Extending BIM continuity from preconstruction into building maintenance is something we have done on a few projects and expect to see more of in the future,” said Matthew Verst, vice president of cost planning and estimating at Cincinnati-based Messer Construction. “Especially when people start to see the increasing value from preconstruction in driving quality and safety, even for maintenance and operations personnel.”
For Alford, extension of preconstruction collaboration tenets into building ops is another example of the blurred lines that could help dissolve traditional discord and disagreement across full project life cycles, particularly in the first year of use.
“The experience of a project is always created in how it finishes, and we want our clients to have successful buildings that operate well, that work the way they were designed,” Alford said. “The satisfaction of the experience is significantly higher when you do it right like that.”
Bumps on the preconstruction path?
The one area for concern shared unanimously by preconstruction professionals as the practice evolves is a human one: the possible lack of stamina amongst subcontractor and specialty trades in adapting to new project delivery models and the onslaught of technologies needed to support them.
Indeed, many subs are already struggling to staff up crews or even bid on new jobs as they clear pandemic-driven backlogs and pivot to new projects.
“People think about long lead supply chains, or material cost escalation, but one of the biggest factors that doesn't get enough attention is the impact of that backlog on the subs and their difficulty getting labor,” Verst said. “It is tough to get competitive bids on scopes, so strong subcontractor relationships are going to be a big key to the success of future opportunities.”
Doing more with less
Like many facets of construction, AI and robotics might ultimately help alleviate labor strife and the continued pressure it exerts on project costs and scheduling, as well as other technologies.
For instance, Miller Construction in Ft. Lauderdale, Florida, adopted Agtek estimating software to save $500,000 on one project by lowering a building’s elevation by 6 inches. Meanwhile, Dusty Robotic’s drywall automation tools, used by McCarthy and others, have helped address labor issues on jobs, an example from the subcontractor community as a way to do more with less.
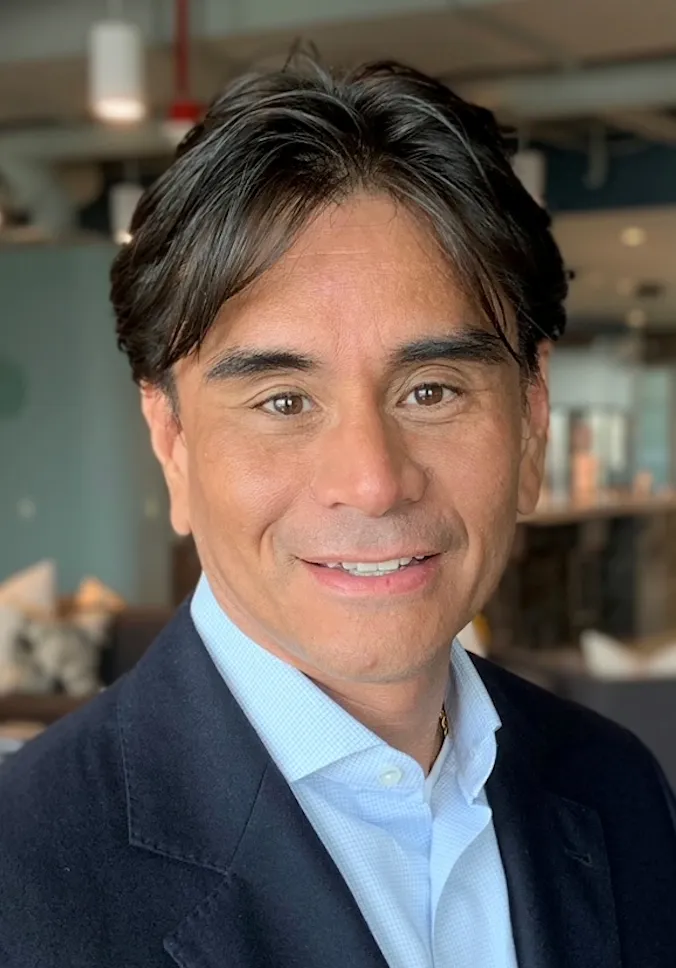
Those are just two examples of new approaches preconstruction teams have incorporated into the process since the pandemic forced a change in project collaboration and perspective.
“Technology will change how we do things, and I’ve seen it change things ever since I’ve started in the industry,” said Eric Orquiola, director of preconstruction at Denver-based PCL Construction. “Whether efficiency is found in technology or lean delivery or whatever else is out there, we need to change processes to meet client needs, because we can’t hire as fast as the projects are coming in.”