Images of the battered Sanibel Causeway in Florida became a symbol for the destruction Hurricane Ian wrought at the end of September. But on Oct. 19 — well ahead of the Oct. 31 target date — the 3-mile-long span reopened, allowing Sanibel Island's 6,000 residents to again come and go freely.
Although Jacksonville, Florida-based Superior Construction regularly does hurricane repair work, pulling off this complicated job so quickly wasn’t easy, according to Division Manager Ryan Hamrick, who helped lead the project. Superior worked in a joint venture with the Miami-based de Moya Group, and Florida DOT contracted the JV for a progressive design-build of the second stage of the project as well: to make the bridge more resilient so an incident like this doesn’t happen again.
The work is being conducted through a progressive design-build contract, and the final cost is not yet available because the design is not finalized. Florida DOT has not yet fulfilled a Sunshine Law request from Construction Dive for information about the contract.
Getting the Sanibel Causeway back in working condition entailed a slew of unique challenges, starting with the jobsite itself. There were two large roadway sections that had to be rebuilt, as well as five approach slabs and areas on two connecting islands — but before it could even access the area, the team had to clear away debris.
“There were just so many challenges with the conditions how they were. The pictures really don’t do it justice. When we get to site, first day, there’s just stuff everywhere,” said Hamrick. “You can’t even access the whole jobsite. You had to get in a boat and go from section to section because of the washout.”
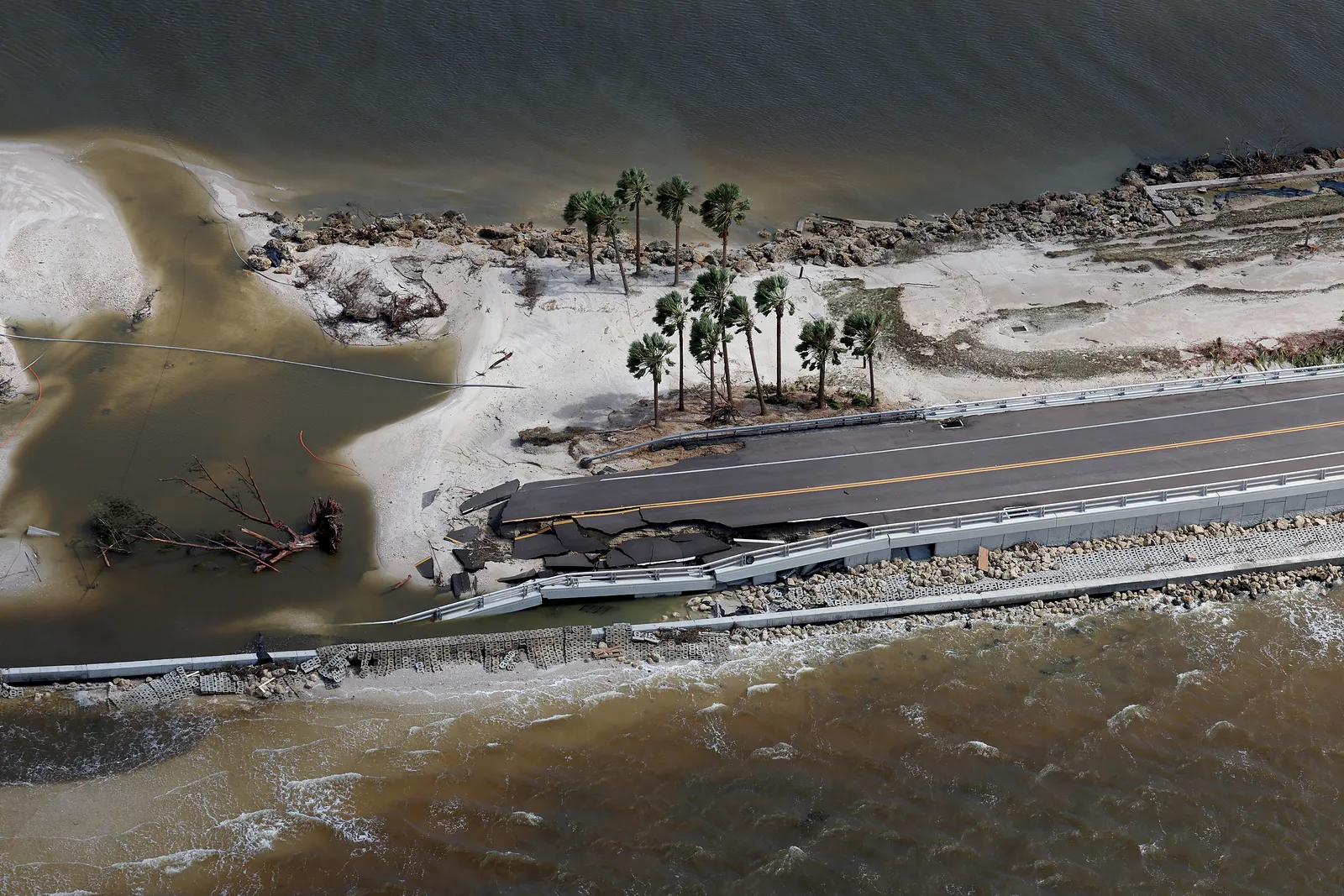
With local businesses out of commission, the contractors had to piece together alternative ways to feed and house about 150 staff. First responder groups offered lodging, and Superior’s team leaders even pitched in by cooking meals.
“Everyone had to work together to overcome these things, because if you’re all pulling in different directions, it’s not going to work,” Hamrick said. “Really no one had this attitude of ‘that’s beneath me’ or ‘I’m not doing that.’ They would do whatever they needed to do for everybody on the job.”
Tech support
Communication is key on a job with so many moving parts, but cell phone service barely worked at first, Hamrick said. Contractors were able to join an emergency response network, and later a Starlink satellite restored internet and cell service to the area. Power was knocked out for the duration of the job, so work had to be done entirely with generator energy.
Crews dredged up material to rebuild the causeway islands, and brought in rip rap and other materials from around the state to fill in washed-out areas. North Venice, Florida-based Ajax Paving repaired roads nearby through a separate contract with Florida DOT.
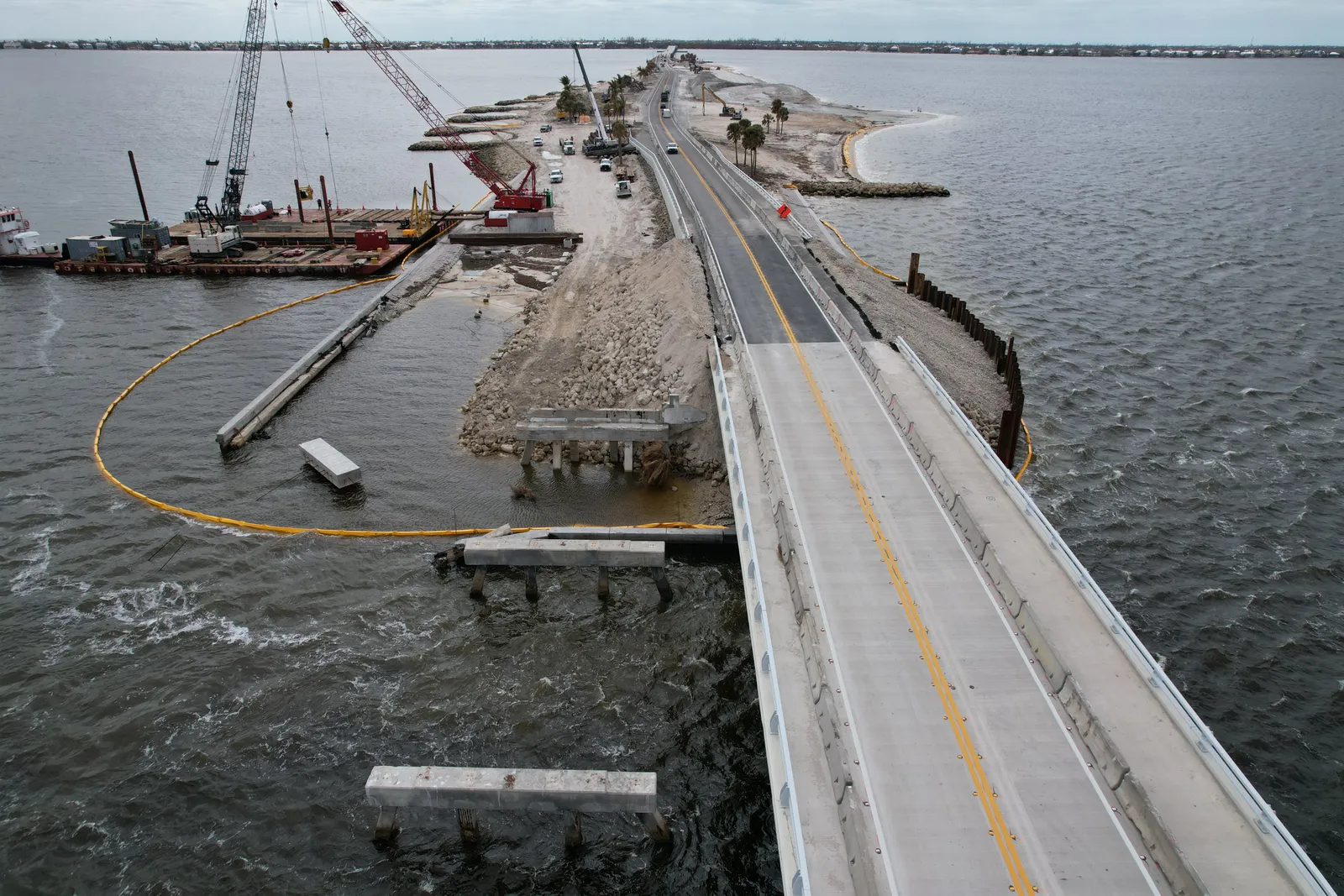
Air force
Thankfully, the team had access to a plethora of resources, including underwater survey equipment, barges and especially, drones, which offered an invaluable view of the lengthy, water-spanning jobsite.
“Having our drone folks down there as frequently as possible was a huge plus for us,” said Hamrick. Drones made it easier to track progress and do quantity checks as fill was brought in to repair areas that had been washed away. They also offered a “visual of what’s being brought in from a larger scale, 10,000-foot view, to really see the whole causeway being brought back up,” Hamrick said.
DOT also used drones, both onsite and from the office in Tallahassee to keep tabs on the work. “It was helpful for everyone involved just to see the jobsite from a higher viewpoint,” Hamrick added.
Lessons learned
In the end, after working around the clock, the teams were able to complete the fixes in only 15 days. Hamrick shared some lessons learned from the job that help make work in a disaster situation a success.
- Clear communication: “The biggest part of that was just open communications throughout the process,” Hamrick said. “As you can imagine, there are people everywhere trying to help, and even though everyone is trying to help, they’re not always as helpful as they try to be.” Frequent meetings between contractors and Florida DOT, emergency responders and others were critical.
- Do your job: “Find out what your specific task is and do it to the best of your ability,” said Hamrick. “Trying to do too much tends to not be productive. You can’t be passive, but you can’t be overly zealous, either. You have to understand what your client needs. In this case, DOT needed us to do a specific job and to do it safely and quickly. We identified what that was, and we poured every possible resource we had into that.”
- Leadership: “It boiled down to leadership from the very top. DOT had key people onsite from all different districts throughout the state, so they really took a commanding lead of the job,” said Hamrick. This all ‘hands on deck’ mentality, he added, filtered to everyone onsite.
Now the Superior/de Moya team is designing options for resilience upgrades to submit to Florida DOT and Lee County, and is prepping for the second stage of the project, according to Hamrick.
The upcoming work will likely involve elements like building out seawalls and elevating parts of the causeway. The timeline isn’t clear, but designs will likely be submitted in the next few weeks and construction work will almost certainly take longer than the first phase, Hamrick said.
For now, the team can take a moment to celebrate their collective success.
“Everyone had a single goal in mind. Everyone knew what they were aiming at, and everyone did everything in their power to execute that, from the top of DOT all of the way up to the governor's office, everyone had one goal in mind: to restore traffic to that causeway,” said Hamrick. “It was something to see how it came together so quickly.”
This story has been updated to clarify information about the contract.