Jennifer Wooles, the director of the virtual planning and construction group at North Reading, Massachusetts-based Columbia Construction, had her work cut out for her.
Ahead of her was a life sciences project that called for 60,000 feet of linear process piping – over 11 miles worth – that had to be installed on a quick time frame.
The renovation of the 60,000-square-foot 1980s facility that would be used for vaccine production presented a thorny issue that made it incredibly difficult: The piping was complex, and the Boston-area facility required intense specialization.
In addition, the site included three different processing labs with mezzanines due to all the equipment. Wooles said that because everything was so complex and specialized with the project, there were issues with using traditional methods.
“2D drawings just weren’t cutting it,” Wooles said.
She turned to as-built, reality capture technology from New York City-based Avvir to help with the layering of the piping, starting work with the company in September 2021 and ending in May 2022. The firm’s software, Wooles said, took a heavy burden off of her shoulders.
Once a week, the team would go through the building with a LiDAR scanner, which uses lasers to gather spatial information about a given area. The scans would be sent to Avvir, and then the team and stakeholders would be able to view the finished product — a combination of the customer-provided models and reality-captured data.
The program is capable of viewing the LiDAR scans and the plans together, and can compare the as-built version to the planned version of the build.
Pipes in 3D
Avvir, which bills itself as offering "BIM-focused reality analysis," counts other contractors such as Skanska, AECOM and DPR as its clients. Wooles’ team used the software to check their build and, particularly, the placement of the pipes. The software can be accurate up to lengths of ⅛ inch, and can tell if the layout of a pipe deviates from the plans in the way it's installed.
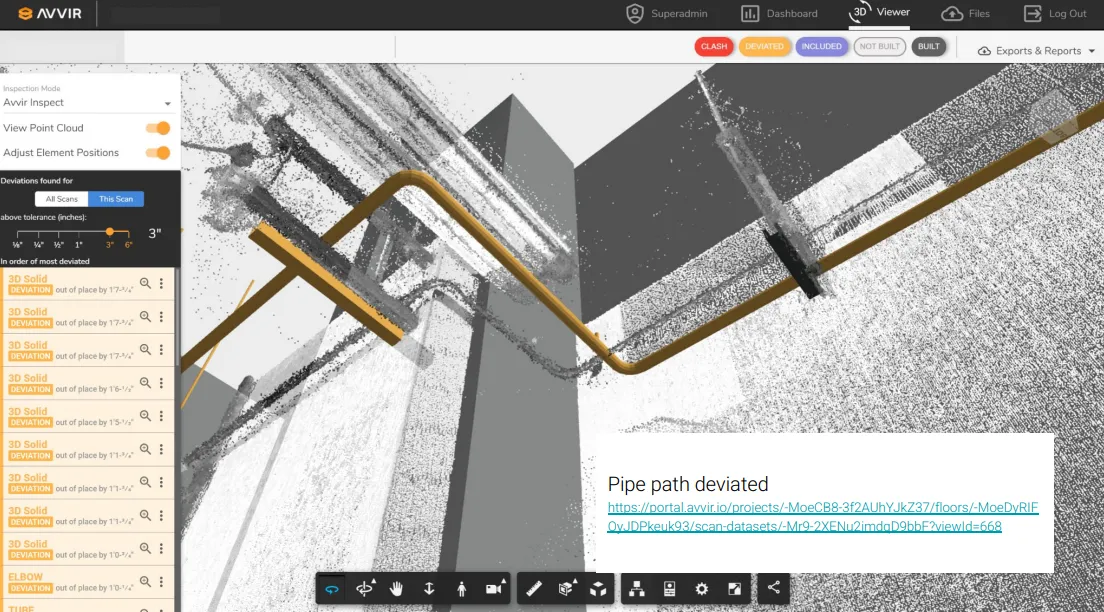
Columbia also used the software on a second project in Cambridge, Massachusetts. Wooles said that the data helped foster a collaborative environment between the second project’s involved owner and the Columbia team.
“Being able to grab and pull the chart up and show them in the model that, ‘Hey, this is the piping that still has to [be installed],’ that was a huge benefit,” Wooles said.
Across both projects, superintendents saved three days per week on creating reports and site walkthroughs and inspections through their usage of the program, according to a Columbia/Avvir case study. Additionally, the software helps Columbia find hiccups and issues that need immediate attention.
Wooles said the projects that benefit most from Avvir are the most complex ones, and that the Columbia team is having discussions on what fits best for each project.
Data challenges
There were some pain points initially, Wooles said, as a result of sending so much data out to users, and a steep learning curve at the beginning, Wooles said. However, once the system was hammered out, the environment became collaborative.
“There's a little bit of a growing pain in the process, but I think that that almost bonded us to be able to slip different ideas off of each other and have a [good] comfort level. If I wasn't keeping up with them, or if they needed to do something for me, then we had this open dialogue,” Wooles said.