Paul Nassetta doesn’t retire well, he says.
After winding down his career as chief operating officer at Washington, D.C.-based contractor Hoffman and Associates, Nassetta returned to the workforce in 2018 as director of design and construction for Johns Hopkins University.
In his new role, Nasetta was tasked with delivering a challenging project: transforming the recently closed Newseum just blocks from the U.S. Capitol into a state-of-the-art higher education facility, along with general contractor Clark Construction.
Dedicated last month, the $300 million JHU Bloomberg Center is a 350,000-square-foot, 10-story academic building on Pennsylvania Avenue that features 38 classrooms, a lounge-style library, a multimedia study, informal study spaces, a 375-seat theater, conference center space, a banquet hall, a fitness center and a rooftop terrace.
The project team began designing the Bloomberg Center in the spring of 2019 with a strict opening deadline for the fall 2023 semester.
The fast-paced timeline and unique building constraints precluding any use of a crane would already be a tall order. Then, the COVID-19 pandemic hit, bringing supply chain snarls and skyrocketing material prices.
Thankfully that didn’t hold the project team up.
“This is a project that on normal terms would've taken an additional year to build,” said Matt Vaughn, project executive at Bethesda, Maryland-based Clark. “But given the constraints, we worked with Johns Hopkins and the design team to create a phased design sequence that allowed us to begin demolition and construction a full year prior to the completion of the overall design.”
Due to work beginning in earnest even before architects Ennead, Rockwell Group and SmithGroup finalized designs, Vaughan said Clark and Johns Hopkins secured and locked in a third of the project costs before COVID hit, which ended up partially protecting the job from inflation.
Careful work
The Newseum — which opened in 2008 — had a massive atrium that held a helicopter and a suspended jumbotron, as escalators and platforms guided visitors around the perimeter, showcasing aspects of journalism history and the evolution of media.
That didn’t exactly translate to a university building.
“We had to pretty much tear out all of the floors below the eighth level,” Nassetta said. “And so in order to do that and keep the building stabilized, we had to put a million pounds of temporary steel in, in the interstitial spaces where the new floors were not going to go.”
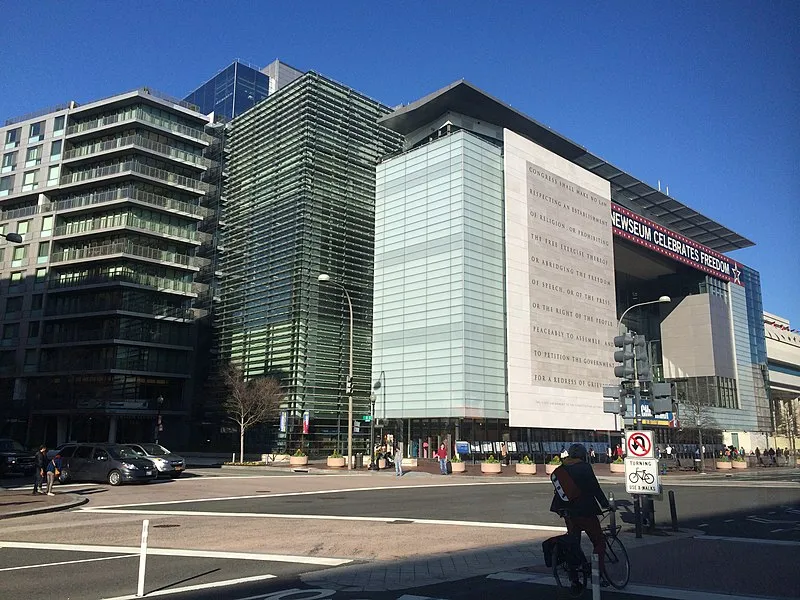
As crews demolished areas below the eighth floor for replacements, they needed to remove broken material and bring in temporary supportive steel for the upper floors. However, due to the complex nature of the design, the roof of the building had to remain intact.
“And so that means that unlike nearly every other complex construction project in the nation, this project would have to be built without the use of a crane that would supply materials from overhead,” said Vaughn.
Instead, crews had to remove the glass facade facing busy Pennsylvania Avenue in order to transport materials in and out and to make space for work.
Lack of uniformity
To update and expand the elevator bank in the building, Nassetta said, the project team built a box around the existing elevators, where concrete subcontractor Miller and Long poured shotcrete around reinforced steel to encase the space. Essentially, the crews constructed a concrete tube, then demolished the elevator work inside and panned out the materials without a crane to then construct a new elevator space, all while working around the tons of temporary steel.
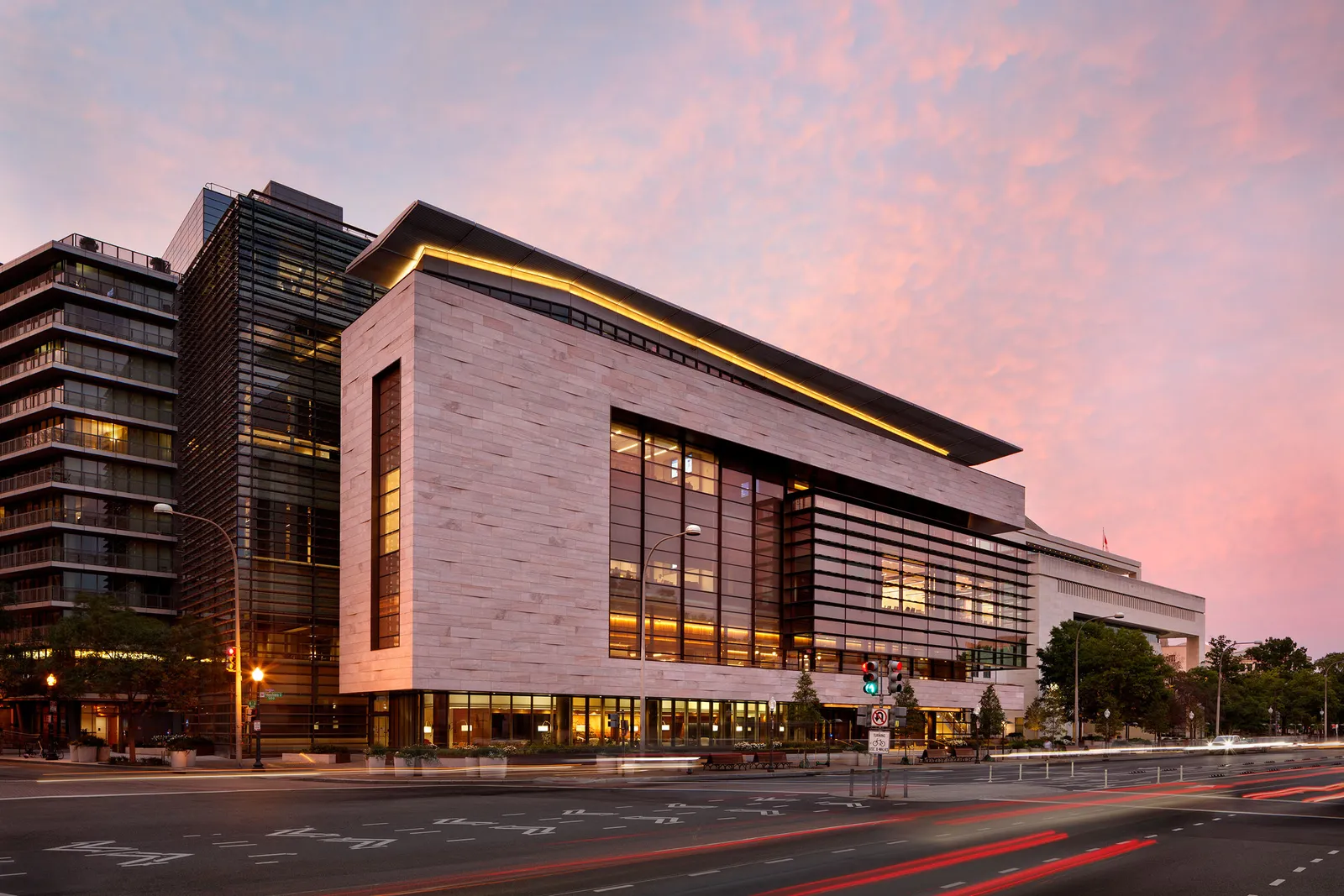
“It was quite a challenge,” Nassetta said.
The new performing arts space is built at the location of the original Newseum theater, which screened IMAX and 4D experiences — not what Johns Hopkins needed. The team had to remove a major post-tension beam and cables, which meant crews used major hydraulic jacks to lift the building up in order to remove the beam, replace it and shrink the theater from 535 to 400 seats.
Vaughn said the lack of uniformity to the project posed the biggest challenge for crews. In many similar jobs, workers begin to get a sense for the structure and rooms or stairwells repeat, which creates familiarity day to day. On the Johns Hopkins project, there was little repetition.
“And so as a result, all of the craftworkers when they built the room stair, they could become experts at the conditions on level five in the room stair, but those conditions would never happen again because on level four or level three, the room stair would be doing something completely different,” Vaughn said. “And so that just meant that our contractors had to really especially be prepared to keep on building these unique conditions.”
The number of workers on the project peaked at over 700 a day, Nassetta said. At first, the project began six days a week, before it secured special permits for work 24/7, which was needed to deliver the project on time.
The challenging nature of the buildout is the exact thing that drew the Clark team to the project, Vaughan said. As for Nassetta, asked if he’ll get better at retiring, he said, “No. I mean, I like staying busy.”