Drew Overmiller is the vice president and design management director at JE Dunn Construction, a Kansas City, Missouri-based construction company.
Opinions are the author’s own.
For the past few years, the labor market has faced considerable challenges, putting strains on project timelines for contractors. Difficulty finding workers is also impacting clients, including those in the manufacturing sector.
More than 74% of manufacturers cited the inability to attract and retain employees as their top primary challenge, according to a second quarter report from the National Association of Manufacturers. This same issue is also affecting industrial clients looking to hire staff once facilities are built.
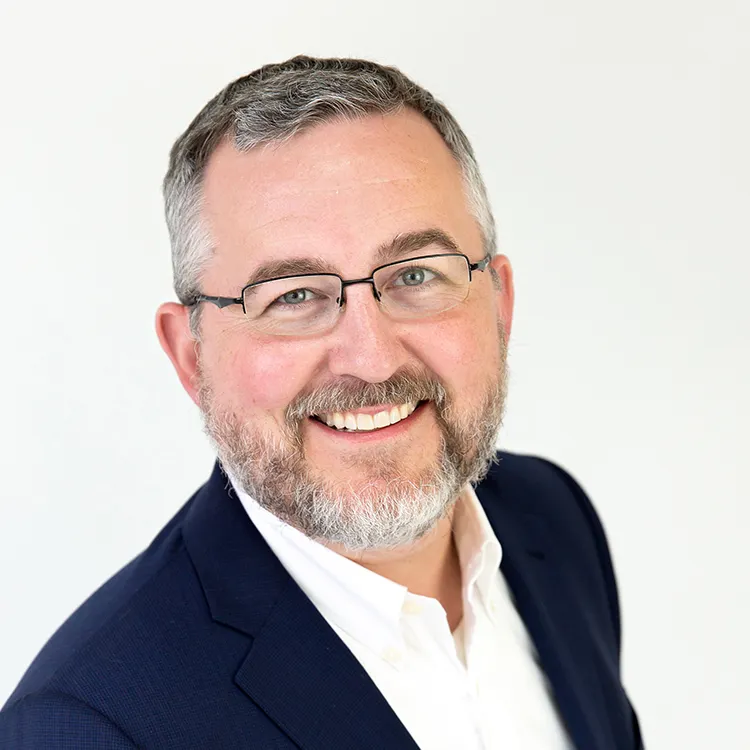
To bridge the labor gap, construction providers have looked inward at their processes to see what can be done differently to create a better built environment, not only for their staff but for the future workforce of large-scale facilities. At JE Dunn, the 16th largest general contractor in the U.S., we have embraced the role technology plays and how modern touches can impact the overall employee experience and eventually the culture at the facility.
Technology starts with design
As technology becomes increasingly integrated into our everyday lives, it is only natural that people seek these same conveniences in the workplace.
To bring these conveniences to industrial spaces, meticulous planning is required to ensure seamless integration. General contractors turn to technology partners during the design process to ensure that a facility’s technology works in harmony and does not create additional burdens for workers.
Our technology partner, Atlanta-based Aptitude Intelligent Integration, designs and integrates systems and services for industrial buildings to create an environment that makes workers want to return. This involves incorporating technology such as automation tools, spot cooling, Bluetooth and power outlets made for mobile devices.
This integration plays a significant role into the built environment, providing workers with the tools that bring ease to their jobs.
The goal with each new design is to envision the space for the end user and to answer a critical question: How can we make the job easier? Keeping this in mind, JE Dunn and Aptitude strongly encourage clients to engage their existing workforce in the design process, as no one knows the job better than the people who perform it.
In recent projects, Aptitude and client IT teams have spent as much as a year gathering information from different departments to ensure all employees’ needs and the necessary technology are considered down to the inch. By offering employees a voice into the end design, workers develop a sense of ownership and pride in their job.
Contractors benefit from tech, too
When it comes to building industrial facilities, technology plays a unique role for contractors in how they bring convenience, drive schedule efficiency and improve safety for their workforce.
The construction industry has seen a boom with the use of cameras, providing workers a new level of vision on projects that was not available a decade ago. Drones used at worksites can be programmed to capture precise video coordinates, showing progress and aiding in future planning. This new perspective has proven to help planners and supervisors spot areas of vulnerability, enabling them to implement additional measures to enhance security and safety on site.
From the sky to the ground, construction teams have incorporated augmented reality into prepping jobsites. Using lasers and modeling tools, workers can gain insight into what lies beneath their feet and mark specific areas of a jobsite, facilitating instruction.
This knowledge significantly improves efficiency and worker safety when a project begins and saves maintenance teams a considerable amount of time.
To enhance safety and convenience while on the move, JE Dunn has turned to software platforms such as OpenSpace. This software platform utilizes a hard hat-mounted camera and captures a complete visual record of the entire project, inside out, which allows supervisors to mark GPS coordinates during walkthroughs. Because of its connectability on site, workers can receive real-time alerts and ensure their safety on-site.
Finishing touches
Advancements in camera technology are also being used as tools to help create a sense of community once facilities are complete.
For instance, the JE Dunn team recently designed a system for a manufacturing client that uses data captured by cameras to show workers their progress and impact to operations. The goal of the system is to provide total transparency to workers and show the employees the value they are bringing to the company. Additionally, based on this data, employers rewarded employees for their performance, fostering a culture of celebration and recognition.
It is also important to create positive areas in high foot traffic spaces. For example, lobbies and employee entrances have become a priority for new clients. These spaces serve as the “first impression,” and starting on a positive note is crucial.
JE Dunn and the Aptitude team have made these spaces welcoming by using monitors and AV systems to inform employees about the day’s events, share announcements and even congratulate employees on anniversaries when they scan their ID badges. These small technology touches allow clients to recognize and show appreciation for their employees’ work.
Looking ahead, it is crucial to recognize the potential of technology to further transform industrial sites.
General contractors are already witnessing the benefits of incorporating technology into operations, providing new levels of convenience, safety and time savings. Employees can now perform their jobs more efficiently and comfortably.
These same benefits extend to clients. By designing industrial projects with employees in mind, construction companies can plan and create spaces with technology that values employees and fosters welcoming environments that attract job seekers.