Matt Hedke is director of VDC Solutions at Southfield, Michigan-based contractor Barton Malow. Opinions are the author’s own.
Advancements in technology often occur after some trial and error, but their success is no accident. Industry-changing innovations require careful planning, a deliberate process and, most importantly, a commitment to innovation and the empowerment to “fail forward.”
Empowering team members to innovate from the top down is critical to continued growth and new ideas, but empowerment without an organized process is not just inefficient — it can be costly, too. We found that while our people continuously pushed the envelope and developed creative solutions, much of it was happening in silos, resulting in pockets of innovation without any framework to maximize it.
That’s when leadership initiated a deliberate effort to develop a scalable process that teams across the organization could repeat, ultimately resulting in more widespread deployment of trials to further change the game.
To ensure efficiency in cost and time it was important to first assemble our Innovation team, which included people from different roles across the organization for initial review of any potential innovation. Our first priority was to create a smaller team with many roles represented to determine metrics for success for the organization and alignment on the project side.
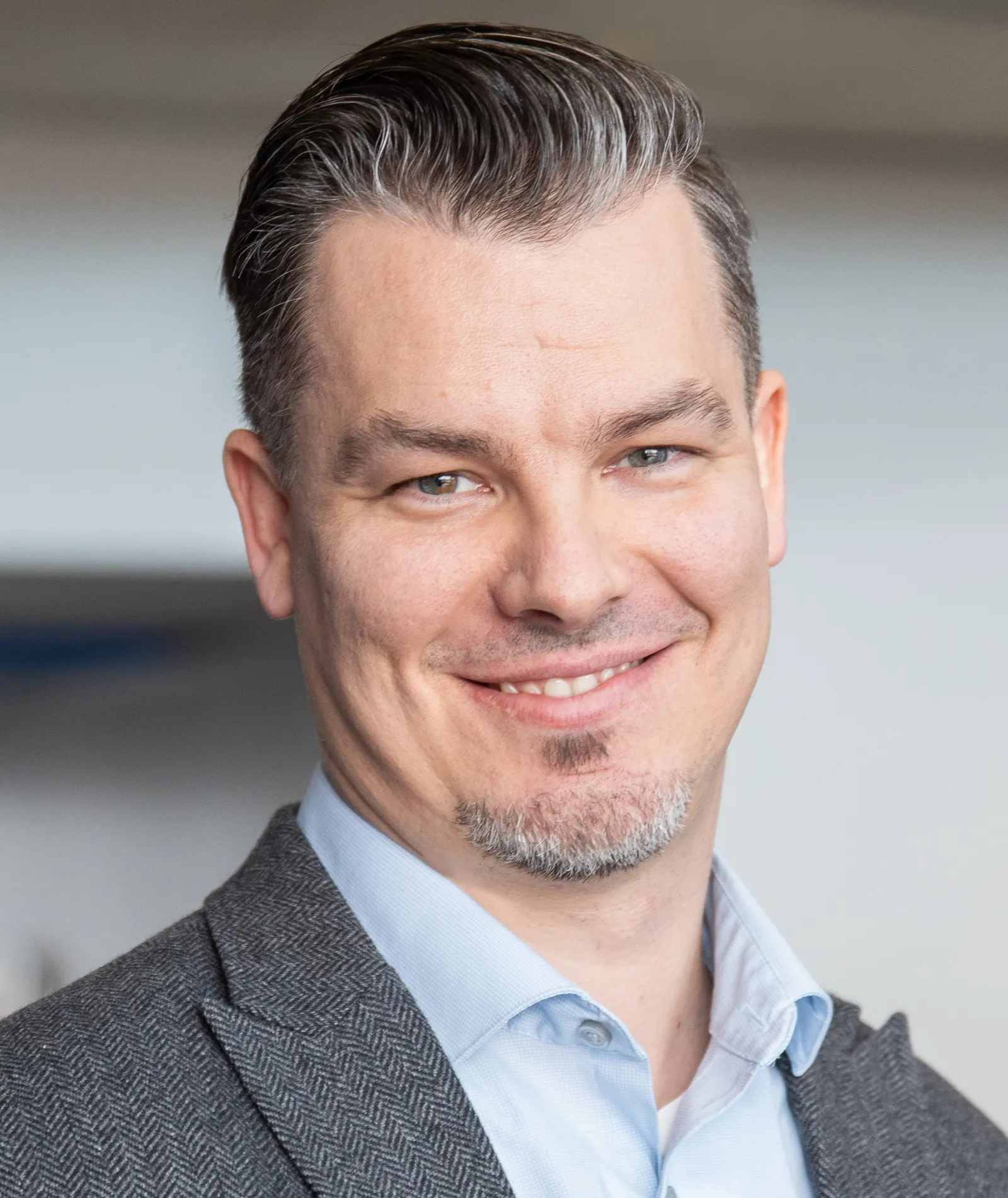
These metrics include potential savings and how to measure them, the effect on factors like safety, cost and schedule, and they can vary from project to project.
Once metrics are set and an idea checks the boxes to move forward, it then goes to a larger group based on the problem, project and proposed solution. This group includes both project and executive team members who work together to pare down solutions before initiating major research and moving forward to the demo phase. If the demo phase is successful, it’s then time to officially pilot the concept.
Before deploying any resources, we ensure there is a clear problem our innovation would solve, get a clear picture of the target audience and make sure all team members understand how we plan to measure success and support the proposed solution. If something checks all those boxes, we deploy it across the enterprise.
Creating efficiency through robotics
One recent technology that is currently being piloted across many of our projects is the use of robotics for laser printing layouts on concrete slabs. Oftentimes, the layout area is condensed and may have some restrictions on the use of space.
Dusty Robotics’ field printer is essentially a laser jet printer that operates much like a Roomba, moving around the site based on inputs from the CAD file created by the VDC team. The team works to identify what needs to be laid out or printed based on project needs (things like interior wall lines, laydown areas, notes and multi-trade layout up to 1/16-inch accuracy) using CAD files from the coordinated BIM model to create the necessary documents.
Once the documents are reviewed and approved, JSON files are sent to the robotic printer, which then follows these documents to print linework on the floor or slab.
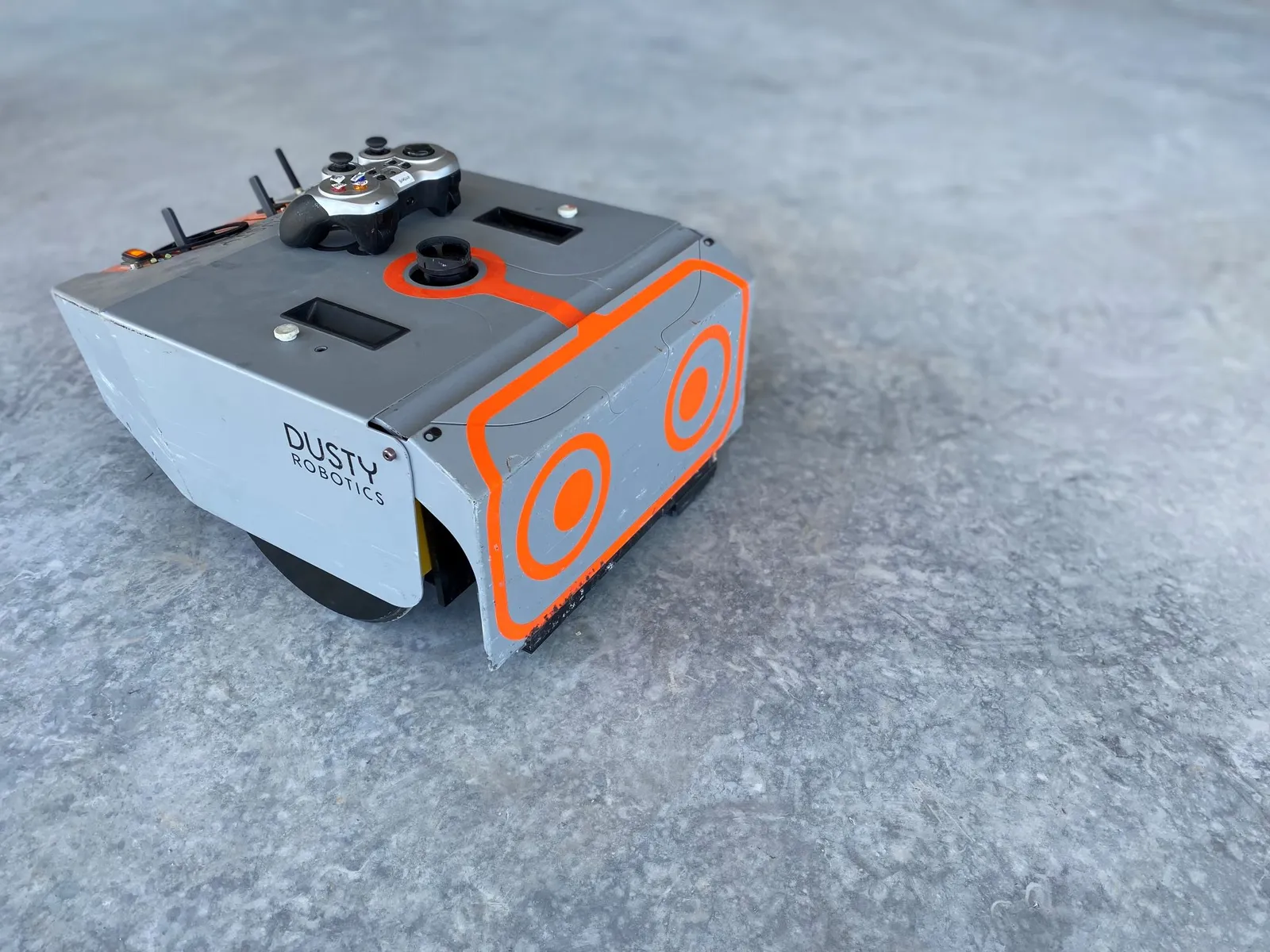
Project teams across the organization are employing this robotics technology and are seeing results with multiple vendors and use cases. Some of these include:
Pre-cast floor layout. Tasked with building at ground level, loading floors with material and lifting that floor into place is a common practice on Barton Malow’s LIFTbuild projects. In a recent project, a laser-printed robotic layout allowed the arrangement on each floor to be completed, including material staging areas, notes and multi-trade layout immediately after floors were cast but prior to the material being loaded on the slabs for the lift.
This was critical to overall scheduling and proved to be a huge benefit not only for preplanning and multi-trade layout but also for enhanced safety by reducing labor on site in a tight area.
Interior wall layout. Leveraging laser-printed robotics for the layout of interior walls has proven to be highly productive as well. Not only does it speed up the layout process, but it also allows for our VDC centralized layout team to scrub the drawings for layout issues prior to being on site. As the team is creating the JSON files for the printer, we are collaborating with the project team on sequence, build plan, potential issues or RFI in the design ahead of time so we can increase the efficiencies in the file.
Using robotics technology, the JSON files were created in two weeks, and Dusty Robot printed 10,700 linear feet of wall line, 972 linear feet of text and 1,071 total text objects in 45 hours of Dusty Robot running time, according to Wade Tolle, centralized layout team member. This is significantly faster than traditional layout methods.
Barton Malow is committed to continuing to test technology on our projects. That includes leveraging innovation to enhance projects as well as benefit our workforce.
When deployed and applied correctly, these innovations have the added advantage of increasing the efficiency and longevity of our people in the field. Finding solutions to improve the bottom line for our clients is important, but so too is maximizing future advancements to help our people innovate the future of the industry efficiently, effectively and safely.