Engineering and construction firm Fluor signed an agreement last month with Longview Fusion Energy Systems, a Livermore, California-based fusion energy company, to serve as its construction and engineering partner in the design and planning of its laser fusion energy plants.
The laser fusion process provides carbon-free energy that can power the needs of a small city, according to Fluor.
The technology ultimately provides process heat or power to drive industrial production of materials like steel, fertilizer and hydrogen fuel, according to Fred Hughes, vice president and Fluor program director for the Longview Fusion Energy Systems Fusion Project.
The partnership aims to demonstrate the feasibility of laser fusion technology and ultimately deliver it to the commercial market, said Tom D’Agostino, group president of Fluor’s Mission Solutions business, in the announcement.
While the site for the first plant under this partnership has not yet been selected, several states and local governments have shown interest, said Hughes. Depending on market demand, Hughes said Longview intends to retain Fluor to follow up on the first plant with multiple electric and process heat facilities.
Here, Hughes talks with Construction Dive about laser fusion technology, its construction processes and the Irving, Texas-based company’s partnership with Longview.
Editor’s note: This interview has been edited for clarity and brevity.
CONSTRUCTION DIVE: What is Fluor’s role in this partnership?
FRED HUGHES: Fluor’s role on this project is as the engineering design partner with Longview Fusion Energy Systems. The conceptual design phase will occur over the next 18 to 24 months followed by the preliminary and detailed design phases.
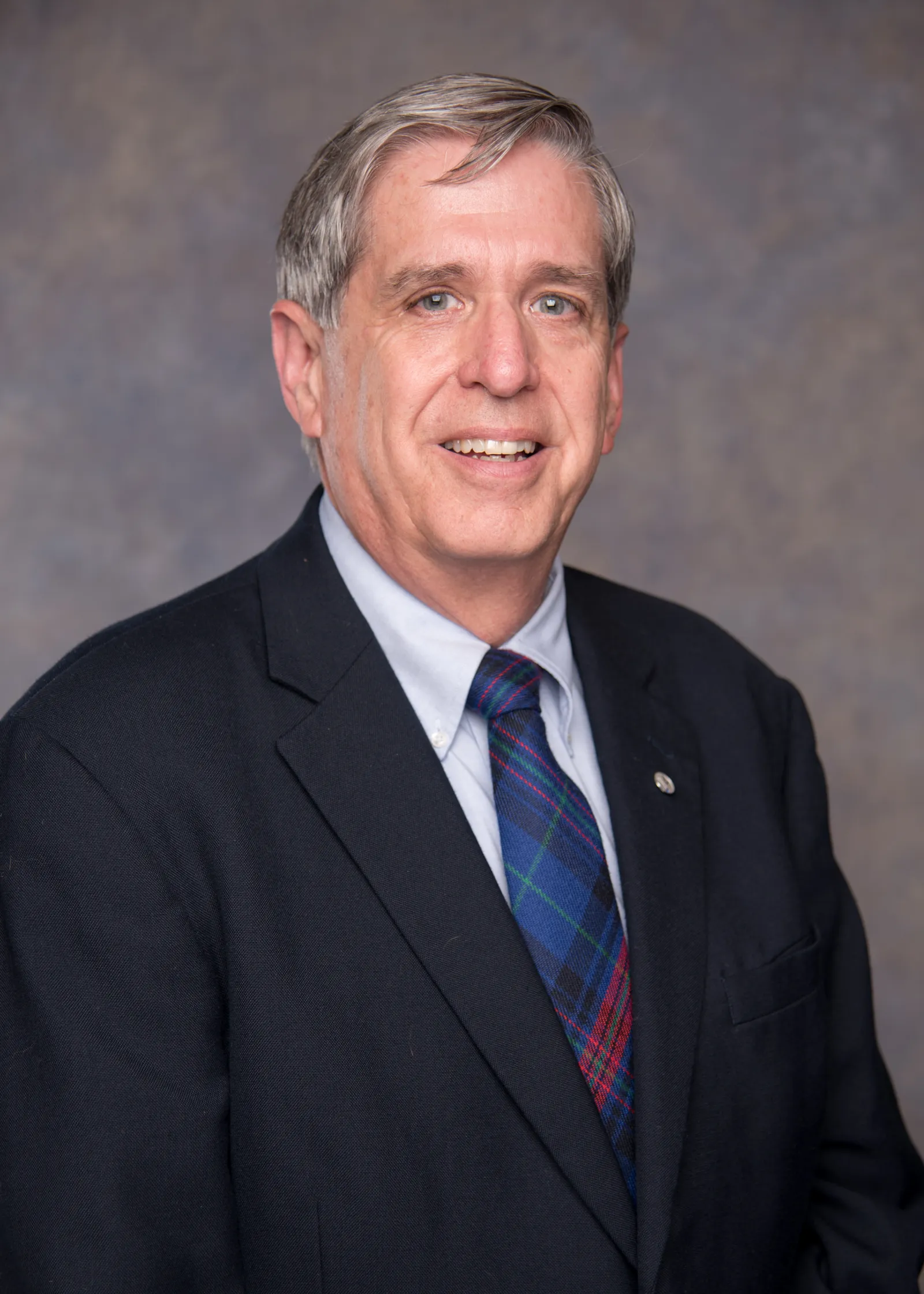
Fluor will also provide regulatory and siting support as requested from Longview. Review gates will be used during the design process to assess the maturity of the design and readiness for construction of the market entry plant.
What’s different about laser fusion power plant construction than other energy facility projects?
There are many.
First, there must be adequate foundational structures to support the fusion engine components and the laser and optical systems and provide for vibration elimination of the laser and engine systems. Second, the design will reflect an emphasis on highly modular construction packages and offsite prefabrication of those packages.
Many of the non-standard technical components will be manufactured offsite as modular plug-and-play assemblies, which we have years of experience implementing.
Third, below grade construction is expected and fourth, there will be significant cleanroom facilities for the laser and fuel manufacturing facility equipment.
In addition, the fusion engine operates within a vacuum chamber. The construction and installation of this vacuum chamber must be closely coordinated with the fusion building erection. Finally, an integrated neutron shielding system will be required for the fusion engine area.
The project will require close coordination between construction and the component vendors to ensure deliveries and integration in support of the overall construction progress.
What are some challenges when taking on these large-scale, complex energy facilities?
The biggest challenge is coordinating the fusion island technology into a cohesive plant design. This requires defining the interfaces among the lasers, fusion engine, coolant and fuel systems, the secondary plant, the control systems, the component designers and the materials experts.
This coordination requires detailed scheduling and frequent communication to resolve issues and ensure that when the plant is constructed, it will operate as designed.
A related challenge with the technology evolving and advancing continuously is designing flexibility into the plant for the anticipated improvements.
This can be overcome with key decision points in the design process where the design is “frozen” to support the overall schedule to deliver the first plant.