This feature is a part of “The Dotted Line” series, which takes an in-depth look at the complex legal landscape of the construction industry. To view the entire series, click here.
Manufacturing continues to drive construction spending, in part thanks to the federal push to onshore chip plants. That means big opportunities for contractors that seek to build these costly facilities, as well as big potential for risk.
The $52 billion CHIPS Act supports companies that build semiconductor factories in the U.S., among other incentives, in an effort to reduce reliance on Chinese-made chips. Dozens of these highly technical megaprojects are have broken ground since the law was signed in Aug. 2022. Many of them are in the billions of dollars.
For instance, the Biden administration awarded Intel $8.5 billion in CHIPS Act funding March 20 for its semiconductor projects in Arizona, New Mexico, Ohio and Oregon, the largest given so far under the law.
Since there are a limited number of specialty contractors with experience in the semiconductor space, some builders are doing this for the first time amid an overall shortage of skilled workers and a raft of regulations. Construction lawyers say given this confluence of events, there are particular areas contractors need to keep in mind when building these projects.
For example, these projects typically require progressive design-build and engineering, procurement and construction approaches, according to Jeffrey Gilmore, chair of the construction practice at national law firm Akerman. They also require heightened security, and workers may need security clearances.
The jobs’ pace and complexity present additional challenges, he told Construction Dive.
“Ultimately, successful project delivery will demand a nimble team prepared to perform very specialized design and construction services suited to the clean building environment necessary for a precision industrial chip facility,” said Gilmore.
Builders must navigate federal regulations
Beyond the technical and logistical aspects, builders working on projects that receive federal funding must also navigate certain federal regulations, such as Davis-Bacon, according to a webinar with Angela Styles and Josh Teitelbaum, partner and senior counsel, respectively, with global law firm Akin Gump Strauss Hauer & Feld. This rule applies to all laborers and mechanics employed by the applicants, sub-recipients, contractors and subcontractors performing construction, alteration or repair work that’s funded in whole or in part with CHIPS money.
While the CHIPS Act does not require applicants to mandate project labor agreements, according to the webinar, they still must provide a project workforce continuity plan in their construction workforce plan that details their efforts to boost workforce development, minimize labor disputes, enhance safety and ensure adequate pay.
All this means it’s vital for contractors to thoroughly understand the risks associated with these projects, and take proactive measures in their contracts to mitigate them.
How to protect yourself
There are key elements that contractors can add to their documentation to make sure they’re bidding effectively and staying compliant. Builders should pay close attention to the definition of the construction project, project costs and payment terms as well as scope of work, said Laura Colca, partner at Baltimore-based Goldberg Segalla.
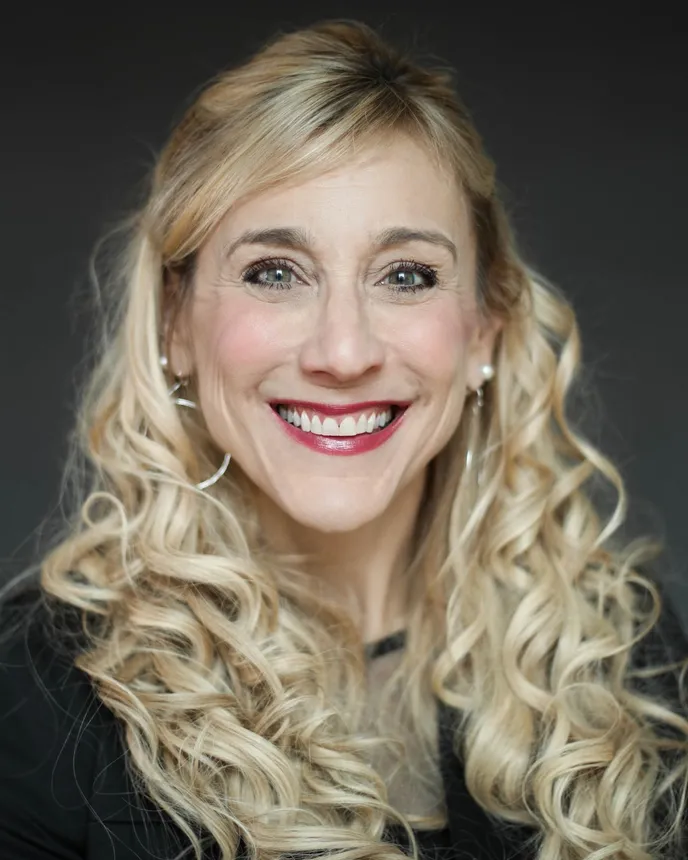
“Having a well-defined scope of work provision can prevent construction delays, cut down on the need for change orders and lessen the likelihood of disputes,” Colca said.
It’s also important that the contract include timelines for all stages of the project. Ill-defined parameters on completion dates open the door for potential conflict, she said.
“A well-drafted work schedule is essential,” said Colca. “Builders should strive for a work schedule that is clear, concise and straightforward as this makes compliance easier and keeps all parties accountable for the project’s progress.”
To further protect against delays, contractors should consider including a “time of the essence” clause that provides that any delay by either party constitutes a material breach, and include a contract term requiring specific notice of a potential delay. Without this, either party may have difficulty recovering for any damages caused by the other party, Colca said.
There are other ways to hedge against unforeseen circumstances, such as a comprehensive force majeure provision that excuses performance if there is a catastrophic event beyond the reasonable control of the parties.
“One final area that should not be overlooked is risk management and liability protection,” Colca said. “Builders should proactively manage risks and use best practices to protect themselves from liability, including monitoring the issues of construction defects, property damage and worker safety.”
____________________________________________________________
The Dotted Line series is brought to you by AIA Contract Documents®, a recognized leader in design and construction contracts. To learn more about their 250+ contracts, and to access free resources, visit their website here. AIA Contract Documents has no influence over Construction Dive’s coverage within the articles, and content does not reflect the views or opinions of The American Institute of Architects, AIA Contract Documents or its employees.