On March 13, 2020, two days after the World Health Organization classified COVID-19 as a pandemic, the U.S. declared a public health emergency.
Uncertainty swirled. Work of all kinds slowed. People isolated themselves, wore masks and worked or took classes on their devices from their kitchen tables, bedrooms or home offices.
“Before COVID hit, we were constantly in the conference room,” said Ray Garfield, co-founder and chairman of Garfield Public/Private, a Dallas-based P3 developer. “Whether it was our place, or whether it was the architect’s or the general contractor’s, all of us were at the table. And then all of a sudden we're not.”
But, as contractors cannot build structures remotely, many projects were deemed “essential,” which meant that in-person activities continued for most construction firms.
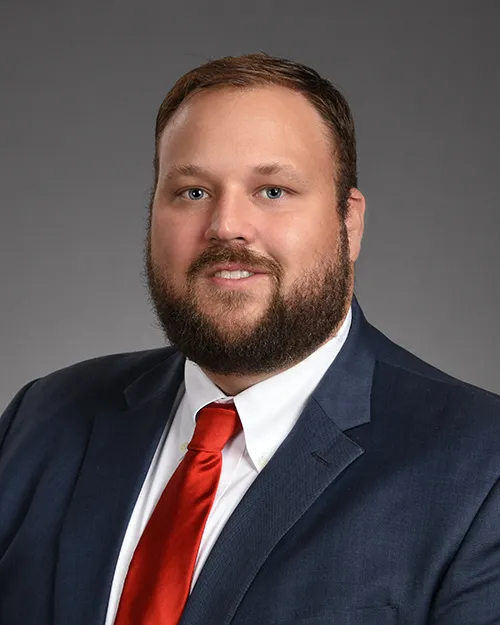
“The fact that construction was deemed essential likely saved the industry as we know it and kept hundreds of thousands of people employed,” said Brandon Mabile, corporate business development director for Baton Rouge, Louisiana-based Performance Contractors. “Had construction shut down, many skilled workers would have been forced to find new employment, and who knows how many would have returned to the industry when work finally resumed.”
At the same time, some projects were put on hold or scrapped entirely, and many workers were laid off as a result. In July 2020, CPWR — The Center for Construction Research and Training, found that nearly 1 million construction workers lost their jobs, with more than half temporarily laid off.
Some chose to retire, a trend heightened the high median age in the industry, while others left construction or potentially chose not to pursue it due to the volatile nature of employment. When the contractors tried to hire them back a year later, workers had become both harder to find and more expensive.
Contractors told Construction Dive that, in the early days of COVID, their top challenge was figuring out how to keep workers safe as building continued. Five years later, the industry is still struggling with the staffing aftermath.
In office or on the job
Garfield described the way his team adapted to working from home as “fantastic.” The change for jobsite workers was, obviously, different.
“The contractors had to be on site breaking ground, putting up steel and concrete. And that was more dangerous for them, more risky. But that was the business that they were in,” Garfield said.
Thomas Murphy, vice president of the aggregates division for Scottsville, New York-based Power & Construction Group, lamented that the rules and guidance for safety with regards to COVID were ever changing, and varied between the state and national level.
"As a utility and aggregate contractor, our employees work in very close proximity to each other on a daily basis,” Murphy said. “The rules being put out by the state were constantly changing, and we would have an executive team call every day at 4:30 p.m. This call would determine how we would do our work the next day and stay in compliance.”
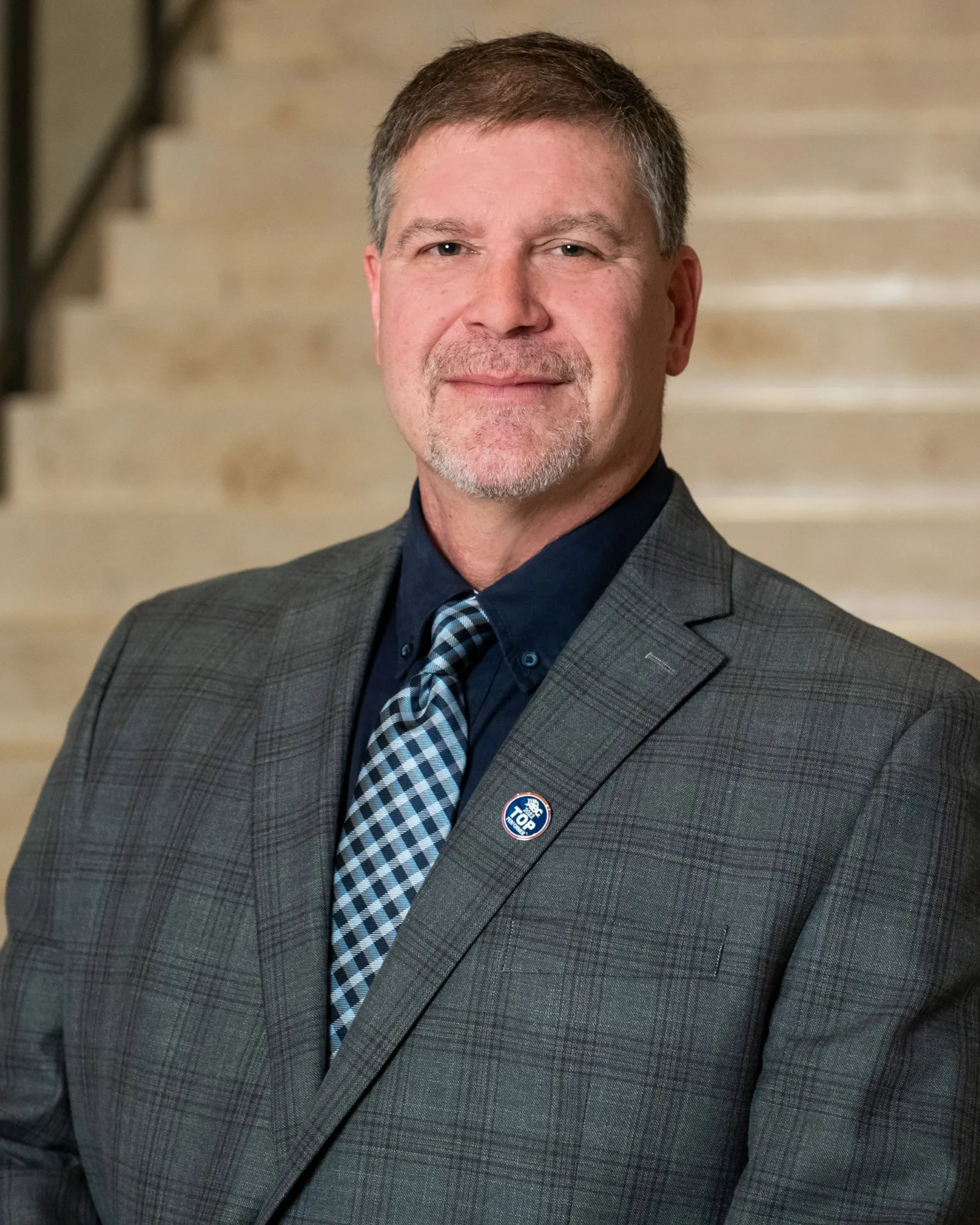
Murphy, whose firm builds electric substations and gas regulators for large power companies, said some jobsite employees refused to work due to their own health concerns, which meant the company needed to find more workers.
And contractors had to plan more to execute those jobs. Mabile said Performance Contractors had to factor in social distancing, health screening and in-demand personal protective equipment.
“We had to learn new ways to work safely in a pandemic environment,” Mabile said. “This included staggering shifts and lunch times to decrease congestion and allow for social distancing.”
For a global firm such as PCL Construction, the challenges of managing complexity and mitigating risks were high. For example, PCL had many jobsites with a high number of craftworkers not directly employed by the Edmonton, Alberta-based firm, with U.S. headquarters in Denver.
“Since our workforce included thousands of hourly trade workers without company email access, we leveraged jobsite signage, daily safety meetings and physical communications to keep them informed,” said Andrew Ahrendt, director of national manufacturing at PCL.
Essential impact
Though Mabile said he believes that construction becoming essential saved the industry, that classification didn’t come immediately, nor was it universally beneficial.
The cost of projects went up, in part due to supply chain issues, but also because contractors had to invest in more resources and expend more time figuring out how work could continue under safety guidelines.
As a result of the pandemic, Performance Contractors had two of its largest projects paused for over a year, Mabile said, which created the challenge of finding new work for employees.
Nonetheless, Murphy noted that in states like New York, construction doesn’t continue at the same clip year round, as the cold winter months can shut down or slow work. Making construction essential ensured the projects could keep moving forward and not face further delays from outside factors like extreme cold or snow.
Lingering labor impacts
The labor shortage existed before 2020, but COVID made it worse, contractors told Construction Dive.
“Some skilled workers did leave for new industries and many others chose to retire,” Mabile said.
The result, Ahrendt said, is that talent retention and recruitment have become “even more critical.”
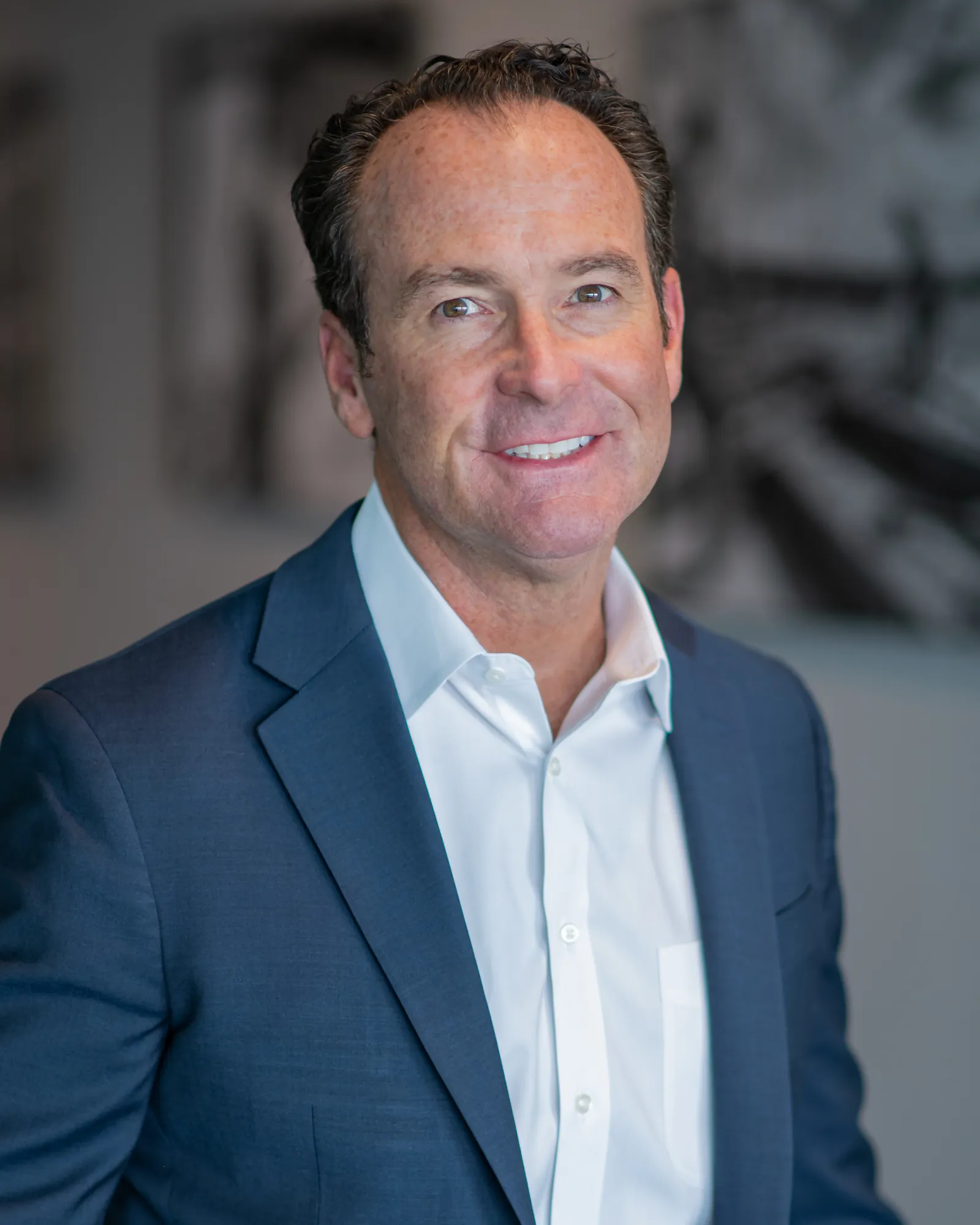
“Labor shortages in the construction and manufacturing industries, exacerbated by the COVID-19 pandemic, have underscored the importance of robust talent retention and recruitment strategies,” Ahrendt said. “By investing in training and development, and promoting a positive and inclusive work environment, we can better navigate the challenges and secure a skilled workforce for the future.”
Correction: The story has been updated to accurately reflect the location of PCL's headquarters.