Construction is a hazard-filled industry. But it is also one contractors, start-ups and tech firms continuously seek to improve by providing new practices or technologies.
In light of Construction Safety Week, Construction Dive asked experts to chime in on the industry’s state of safety, both the good and the not so good.
Here, in a digital round table, is what these experts said.
The following have been edited for brevity and clarity.
CONSTRUCTION DIVE: What is the most exciting thing evolving in construction safety today?
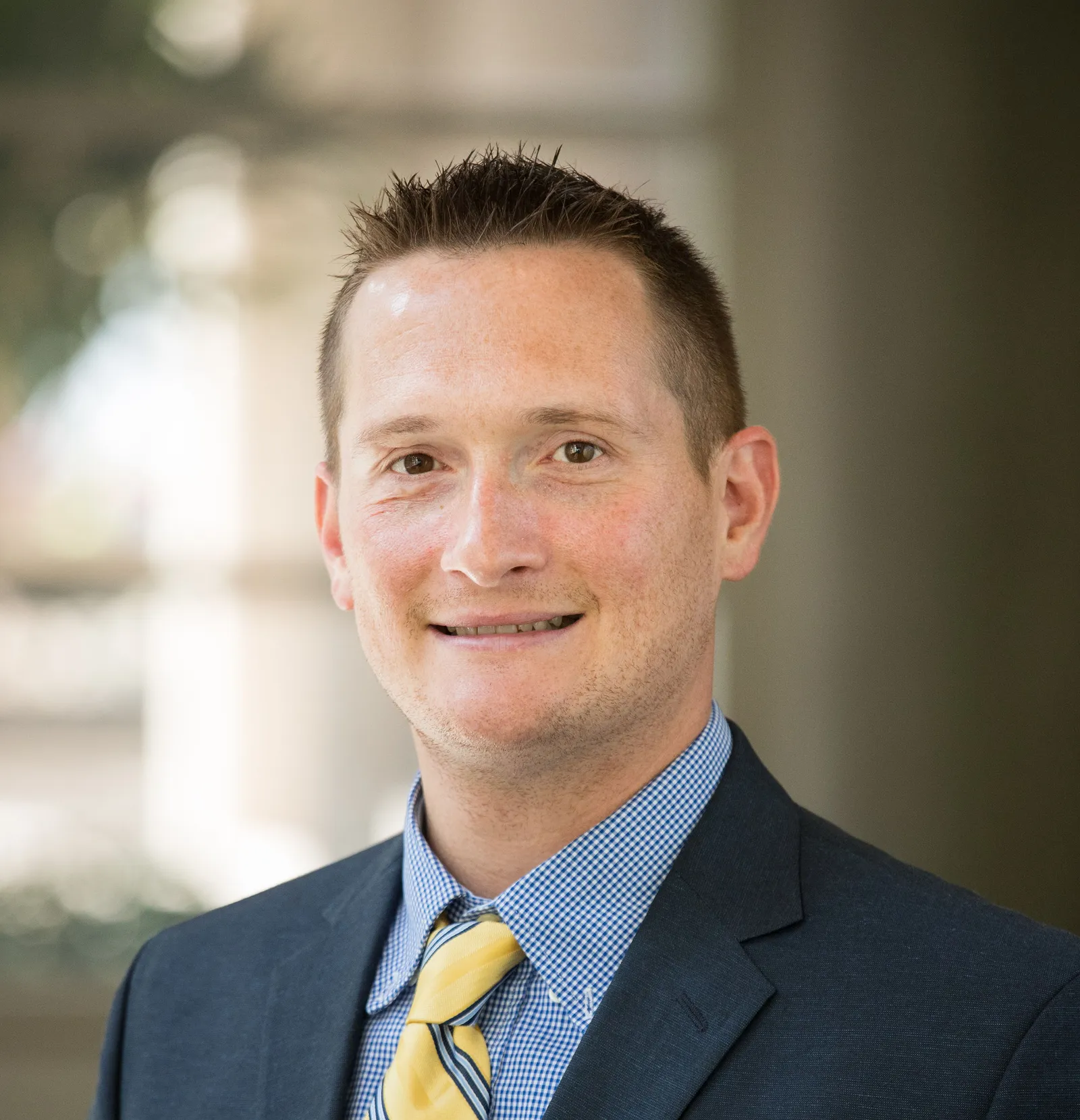
Justin Rihn, director of safety, Clark Construction: One of the most important concepts to receive mass adoption across the industry has been the transition from using recordable incident data as the indicator for our incident prevention efforts and shifting the focus to the Serious Injuries and Fatalities framework.
Since shifting focus, we have reduced total SIF exposures on Clark projects by over 60%.
The investigative findings from SIF exposure tracking and trending have allowed Clark to focus on specific areas of improvement, including falling object prevention, hands-on power tool education and awareness for our teams. Doing so has further reduced exposure to serious injuries or fatalities at our sites, by allowing our teams to zero in on what matters.
Paul Haining, chief environmental health and safety officer at Skanska USA: Digitalization integrated into our workflow has allowed us to be proactive about collecting safety data and using those findings to advance our safety practices and operations across our project portfolio.
Having immediate access to accurate and live safety data findings helped lead to Care for Life 5, a new safety framework at Skanska.
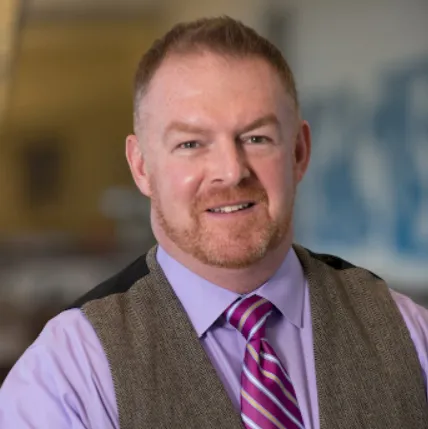
Through the program, we’re able to spearhead more consistent planning and action around our top five job site hazards and because of the availability of increased data, we are able to clearly see where we can enhance safety planning and act on it.
Shaun Carvalho, chief safety officer, Shawmut: As technology continues to improve, its ability to passively analyze and communicate where incidents are likely to occur is becoming even more refined, taking us one step closer to predictive safety and providing us more time for person-to-person interactions.
The data, when fed into the right dashboards and systems, quickly and clearly pinpoints where issues might arise, allowing front line supervisors to take the actions necessary to prevent incidents from occurring.
It also allows teams to spend more time interacting with each other on the jobsite, driving engagement and compliance to build stronger, more connected teams. More interaction leads to problem-solving and candid conversations to ensure everyone feels safe and secure.
Cindy DePrater, senior vice president, chief EH&S officer, Turner: The most exciting thing we are seeing is that as we continue to reinforce the importance of dignity and respect for others, workers are more comfortable talking about their own mental health and physical wellbeing.
We are also seeing that workers are more easily reaching out within and across teams to engage with others and look out for each other’s safety. Our focus on active caring, creating an inclusive environment, and engagement is making jobsites a better and safer place to work.
Richard Ryan, senior vice president of national safety, Balfour Beatty: We believe advancements in technology and their implementation into our operations relies on the tools’ ability to deliver meaningful outcomes that improve jobsite safety and productivity.
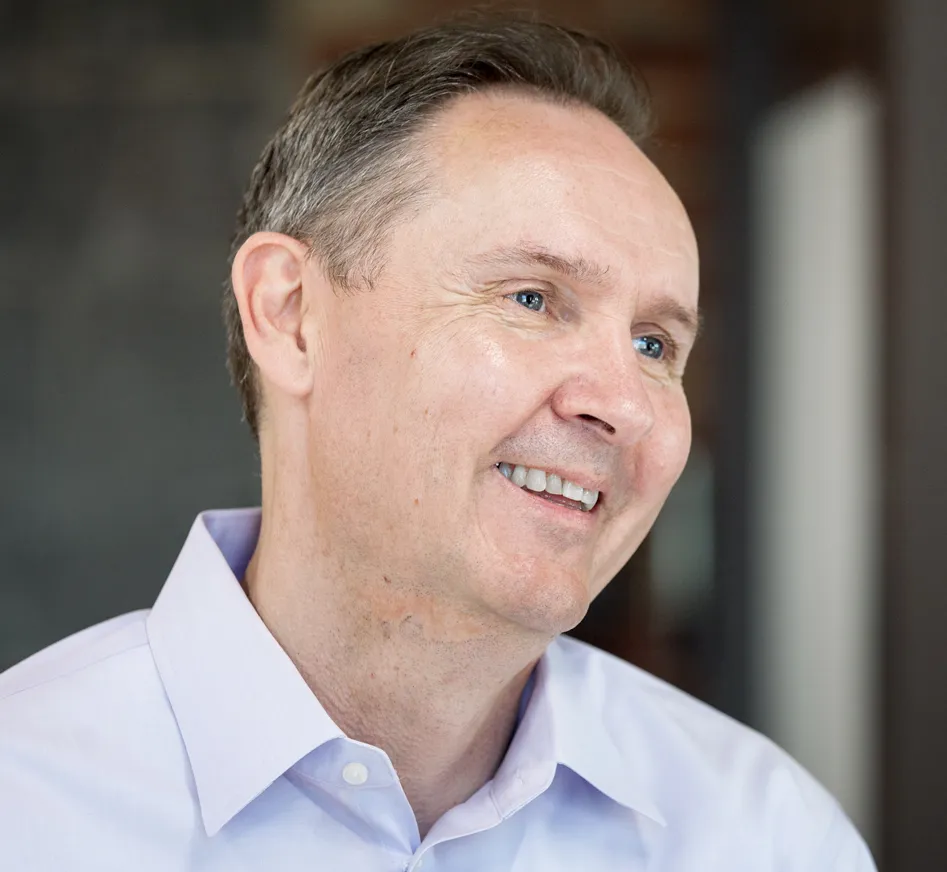
For example, our safety observation technology provides critical insights into leading indicators of incident trends and high-potential or near-miss events that could result in a fatality or life-altering injuries.
Our teams and trade partners use a mobile app to document safety observations in real-time, which is continually expanding and improving our data through artificial intelligence.
Because our culture prioritizes the holistic wellbeing of every individual on our jobsites, we know that any successful safety observation platform must be accompanied by an effective conversation. Whether the observation is regarding an unsafe behavior or action or even a positive reinforcement of safe choices, conversations are vital in empowering the workforce to take charge of safety.
What is the biggest challenge in construction safety today?
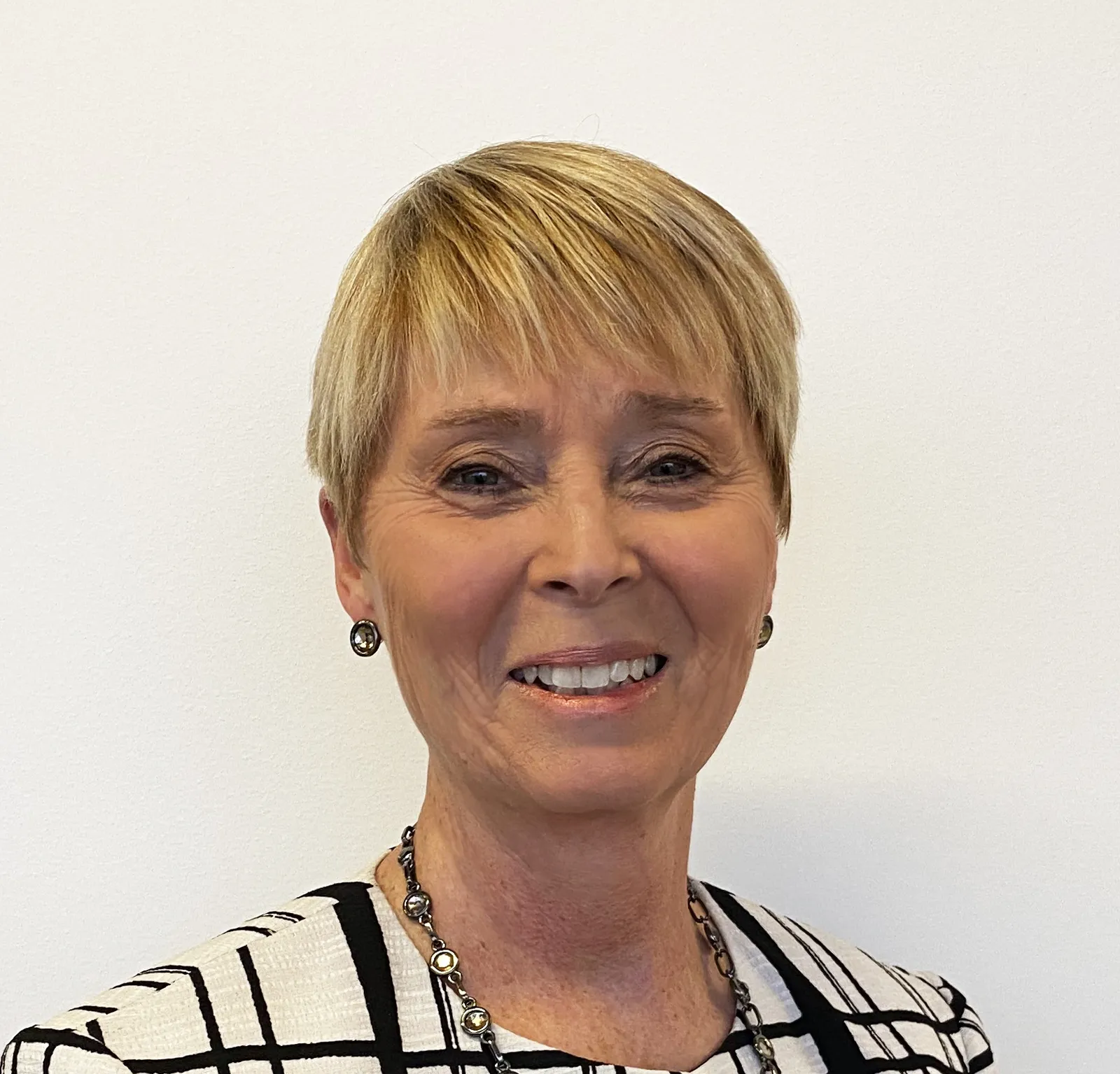
DePrater: The biggest challenge is getting workers who pass through our jobsites to truly believe they have the power to stop work if they do not have the right equipment or safety plan in place to perform a task. We want everyone and anyone to speak up and stop work if there is an unsafe condition, action or safer way to perform a task.
Haining: We need to continue to find ways to collaborate and innovate through safety. When people think of innovation, they often think of enhanced technology as the solution and that shouldn’t always be the case. As it pertains to safety enhancement, reimagining how we can design a specific tool or configure a jobsite to best eliminate a potential hazard in the first place is where more time and energy could be allotted in order to keep our teammates and the industry as a whole safe.
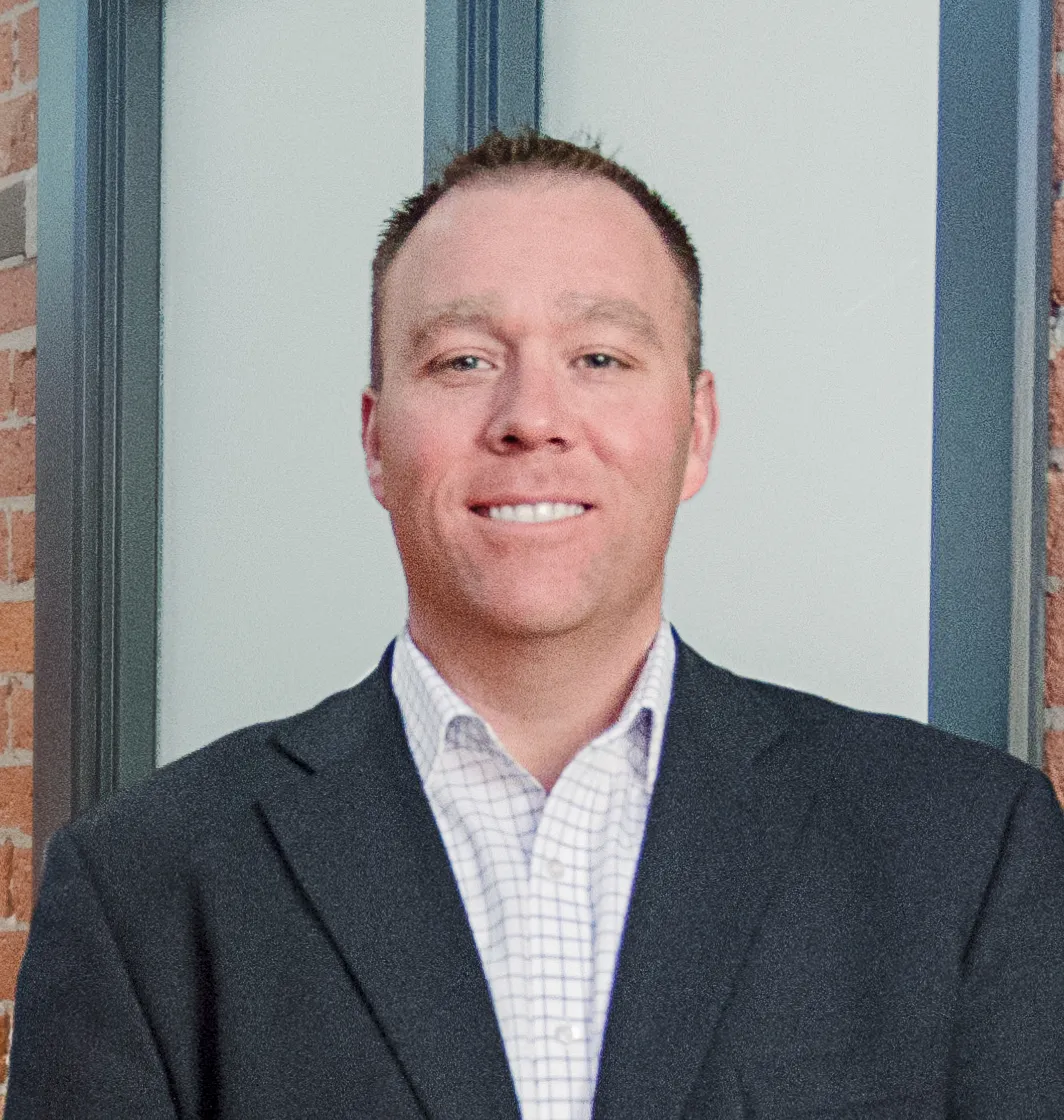
Carvalho: Mental health continues to be the biggest challenge in safety today — more construction workers die each year from suicide and overdose than every other workplace-related fatality combined.
This mental health crisis layered on top of the high-risk work that is required in construction creates an urgent, critical need for a focus on total worker health, supporting physical and psychological health and wellbeing. That focus and effective change starts with top-down leadership, addressing mental health stigmas head-on and integrating mental health into not only the safety program, but company culture.
Rihn: Most people would agree the biggest challenge we’re facing and are going to face is the mass influx of newer, less experienced workers into the trades who need rapid skills training alongside more experienced workers. AGC studies show a significant lag in the number of new construction workers needed to maintain the current hiring pace.
Companies will need to find new strategies to engage the next generation of construction workers by increasing critical training opportunities and providing situational awareness, safety and technical training.
Ryan: Challenges such as worker distractions, fast-paced schedules and tight budgets present an opportunity to approach safety from different perspectives that ultimately improve ongoing safety operations. This includes creating a holistic safety culture that prioritizes the safety, health and wellbeing of teammates and reinforces the importance that each day, the goal is to make it home safely.
Additionally, it is imperative for safety operations to adapt and not be compromised when delivering challenging projects. By leveraging progressive delivery methods such as premanufacturing and prefabrication, teams can reduce and stabilize onsite labor and better regulate schedules.