Gonzalo Galindo is head of Madrid-based Cemex Ventures, the investment arm of the building materials giant. Opinions are the author’s own.
It’s no secret construction faces a skills shortage, one that’s widening as veteran workers retire, project demands rise and sustainability goals add new complexities.
Fortunately, the rise of construction technology has introduced a wave of innovations — from AI-driven project management tools and advanced robotics to digital twin technology — that can help fill this gap by reshaping how buildings are designed, constructed and maintained.
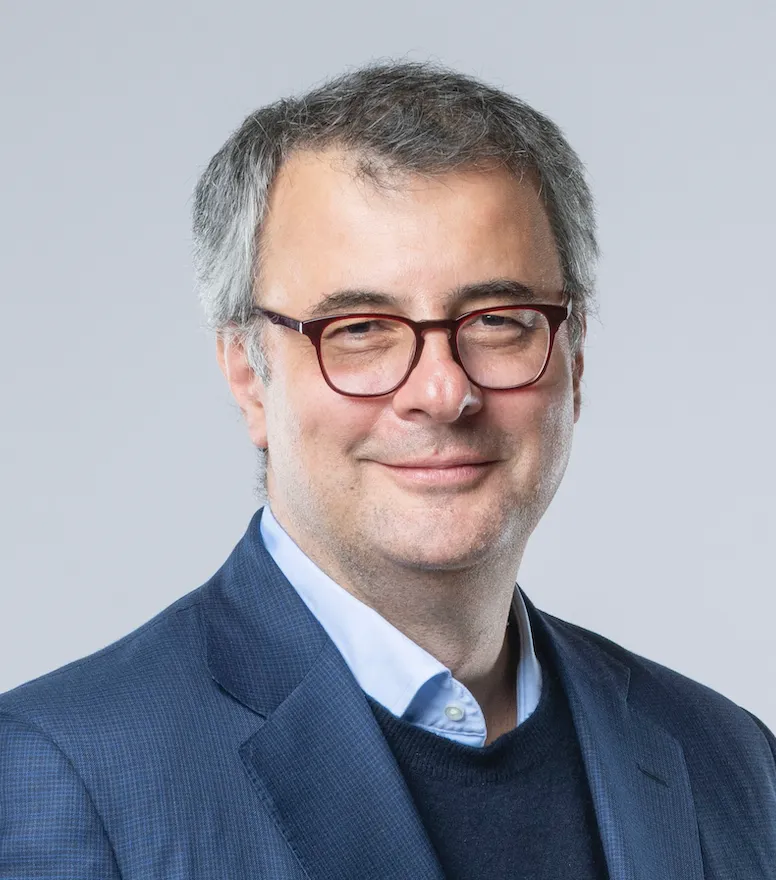
Yet, adopting these technologies comes with its own set of challenges, including high upfront costs, training workers on new systems and managing safety risks. To be successful, we need to balance innovation with practical workforce development.
Minding the gap
Artificial intelligence has emerged as a major focus in construction over the last year, with AI-driven project management software helping teams stay aligned, reduce errors and improve efficiency. These tools centralize project data, ensuring that all stakeholders have access to the same up-to-date information, minimizing miscommunication and delays.
Another way technology is transforming jobsite planning is through real-time process monitoring systems like ObraLink. Traditionally, when pouring concrete for a high-rise building, construction teams must wait 28 days to confirm that the concrete has properly cured. ObraLink’s platform significantly reduces this waiting period by providing real-time data on concrete strength, allowing teams to reduce downtime and keep projects on schedule.
3D printing also shows promise. While still in the early stages of adoption, the technology is being used to print everything from concrete walls and foundation elements to intricate façade panels, customized formwork and even entire small-scale structures. As it matures and becomes more cost-effective, 3D printing could play a key role in addressing skill shortages by automating labor-intensive tasks and reducing the need for large crews.
More advanced automation — such as robotics for on-site tasks — remains in the early stages. Unlike manufacturing, in which standardized tasks allow for efficient automation, construction sites present constantly changing conditions.
For instance, robotic drywall installers and bricklaying machines exist but require recalibration for each project to accommodate different wall dimensions, material compositions and structural layouts. Transporting and assembling these machines across multiple sites also adds logistical complexity, making them less practical for many contractors.
Over time, advancements in machine learning, modular automation and adaptable robotics will help overcome these barriers, making automation more viable.
Start small
Change can be a daunting prospect for both managers and employees, but it’s unavoidable as automation and digital tools transform construction. Those who adapt by developing new skills — such as operating and maintaining robotics, analyzing data from digital twins or managing AI-driven scheduling tools — will find themselves in high demand.
Many construction companies operate on thin margins, making it difficult to justify upfront investments in unproven innovations. To get around such hesitancy, companies can start with small-scale pilot programs that provide concrete benefits before they commit to larger rollouts. Showcasing early wins — such as faster project completion times or improved safety metrics — can help build confidence among both leadership and frontline workers.
Just as architects transitioned from hand-drawn blueprints to CAD software, construction professionals must become proficient in emerging technologies. This transition won’t happen overnight, but gradual integration will ease the learning curve.
Site supervisors may spend less time on paperwork and more time analyzing real-time project data from drones and sensors. Equipment operators might transition from manual controls to overseeing fleets of autonomous machinery.
To support this shift, companies should foster a learning culture in which upskilling is continuous rather than a one-time effort. Investing in on-the-job training, online courses and industry partnerships can ensure that workers stay ahead of the curve.
Future forward
Ultimately, overcoming the skills gap and preparing for the future go hand in hand. As automation and digital tools reshape the construction industry, a collaborative effort will be essential to navigate this transition successfully.
Leadership must take the first step by adopting strategic technologies that enhance efficiency, while workers need access to training that equips them with the skills to work alongside these advancements. When the industry as a whole recognizes innovation not as a disruption but as an opportunity for growth, it will be better positioned to meet both present and future challenges.