It’s been another whirlwind year for the construction industry, and technology wasn’t a calming influence.
The hubbub surrounding artificial intelligence — particularly generative AI — consumed much of the construction technology industry’s focus. Experts told Construction Dive how important the technology would be to the industry in coming years.
Those same pros also emphasized other areas contractors should be mindful of, especially advancements aimed at solving the labor crisis. These include software-based tools that use artificial intelligence as well as robotics and new building materials and processes.
Artificial intelligence
Following the floodgates that opened after OpenAI released ChatGPT last year, experts across industries have been examining how the burgeoning technology will change their work.
“It's the only thing that people want to talk about on panels,” said Kelly Benedict, the head of innovation and transformation for Providence, Rhode Island-based Gilbane Building Co. “How are construction companies starting to use generative AI?”
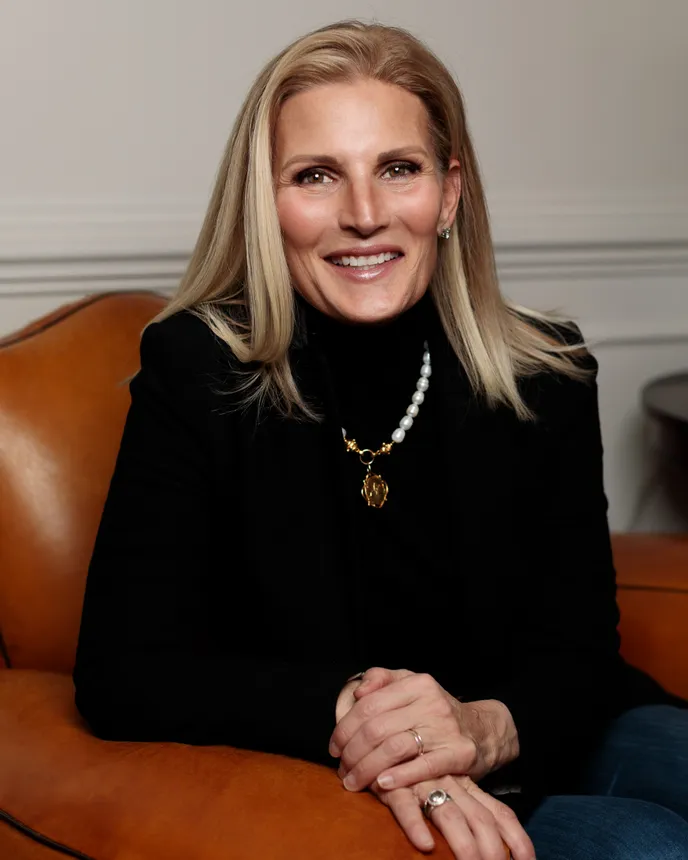
Matt Abeles, vice president of construction technology and innovation at Associated Builders and Contractors, said that the power of AI could be used to free workers from the daily drudgery of mundane tasks, like emails, along with work on the jobsite.
“In construction, we can lean on AI for essential goals like upskilling, workforce development, knowledge transfer, supply chain optimization, enhanced safety design and planning and much more,” Abeles said.
However, these experts also cautioned contractors to be careful. While that’s not unique advice -– the ousting and reinstatement of OpenAI CEO Sam Altman in 2023 revolved around existential threats the tech could pose for humanity — professionals in the building industries need to take particular care.
“In our industry, we really need to be cognizant of life, safety and the risks of our jobs,” said Henning Roedel, the robotics lead for Redwood City, California-based DPR Construction. “If that large language model responds with the wrong answer, and we believe it and act on it, that’s on us. We have to be really cautious about that, and make sure that the information is correct and to do our due diligence.”
Robotics
A topic that often goes with AI, robotics are also front and center in the contech space.

Their applications are varied. Some lay bricks. Some drive piles as part of industrial solar installations. One humanoid robot can move around a jobsite, tossing bags with impressive feats of dexterity and athleticism. Finally, an experimental worksite in Canada was entirely operated by autonomous machinery.
But that may just be the beginning of the rise of the machines in construction.
Roedel pointed to a breakthrough from the Toyota Research Institute, where researchers are using a generative AI technique known as “diffusion policy” to teach robots how to perform dexterous tasks. In the same vein as large language models, like ChatGPT, the goal is to create Large Behavior Models.
“Combining AI with the hardware, I think it could be the big thing in 2024 that will revolutionize our industry,” Roedel said.
An important caveat, however, is the unpredictability of both the tech and what happens on jobsites. Robotics experts have asked industry pros to wait and see when calculating the impacts that the machines will have on their businesses — including whether robots will eventually take jobs from human workers.
Mass timber and prefabrication
Beyond straight technology, innovative materials and processes will also dominate conversations about improving construction productivity in 2024. For instance, an increasing number of owners and municipalities are turning to mass timber as a more carbon-friendly alternative to concrete, steel and other high-polluting components.
Examples include Amazon’s $2.5 billion second headquarters in Arlington, Virginia; two new buildings at Bowdoin College in Brunswick, Maine; and a $150 million mass timber institutional building in Toronto.
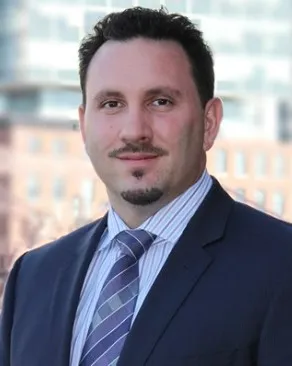
Builders are also increasingly homing in on efficient processes such as prefabrication, while still keeping a healthy dose of skepticism in reserve toward the approach.
“You take some choice out of the equation,” said Michael Zeppieri, vice president of emerging technology at Skanska USA Building. “You can get to volume and economy of scale, and you can meet market need, but you're taking away choice.” As a result, Zeppieri added, final outcomes can be somewhat “cookie cutter.”
For that reason, builders should pick and choose where to apply this process.
“I think our approach is going to be more strategic,” said Danielle O’Connell, Skanska USA Building’s senior director of emerging technology. “We don't just have to do prefab because an owner wants it, but actually being able to identify why that might not work or why it might work really well.”
3D printing
One technology that may still be under the radar for many large contractors in 2024 is industrial 3D printing.
The additive manufacturing method may still be somewhat experimental for most builders, and is primarily in the domain of startups looking to change the way contractors build residential properties, or as a foothold for construction in space.
However, large builders, such as Falls Church, Virginia-based HITT Contracting are also paying attention to the tech — the company is dedicating space in its new headquarters for experiments that include a cutting-edge 3D printing system.
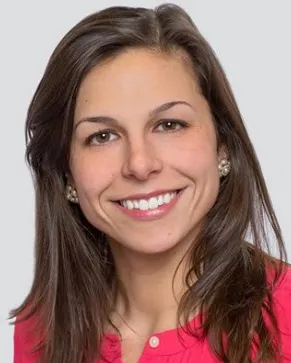
Skanska’s O’Connell said that she has noticed a recent uptick in 3D printing interest, though real commercial results remain further out.
“I don't think we've seen anything at Skanska that's scaled to the point where we could use it,” O’Connell said. “But that could change.”
DPR’s Roedel is more bullish on the technology.
“I think every jobsite is going to have some form of 3D printer,” Roedel said. He differentiated between a small printer, to make custom parts that can be shipped out to manufacturers, to massive installations that can carry out actual formwork.